- Home
- 【Work】 プロジェクトストーリー
- 生産性向上と品質の安定を実現するギヤホーニングマシンを開発 ギヤホーニング盤FX260
Project Story プロジェクトストーリー
生産性向上と品質の安定を実現する
ギヤホーニングマシンを開発
ギヤホーニング盤FX260
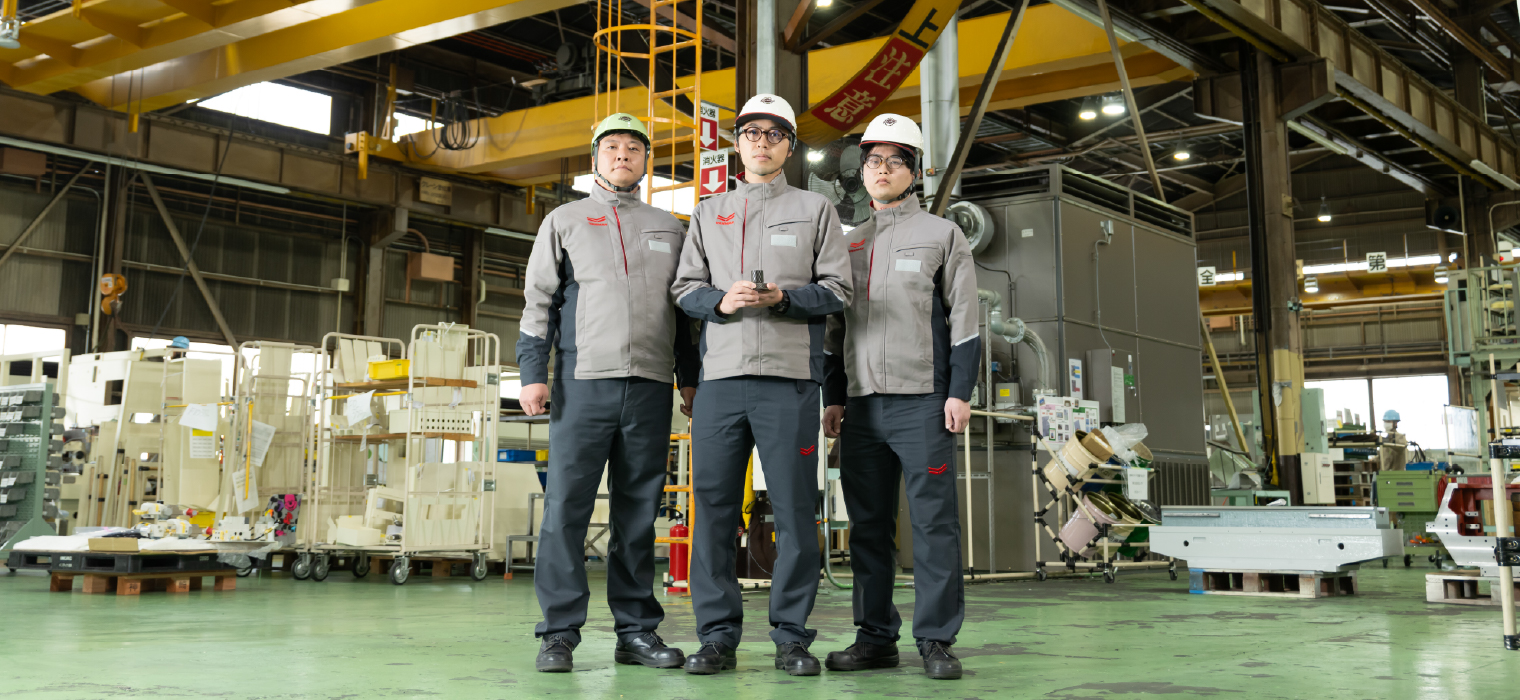
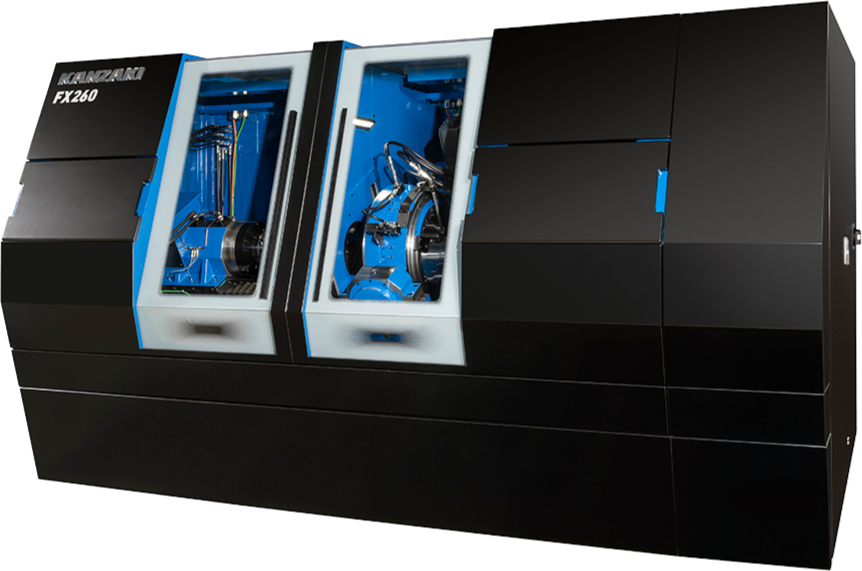
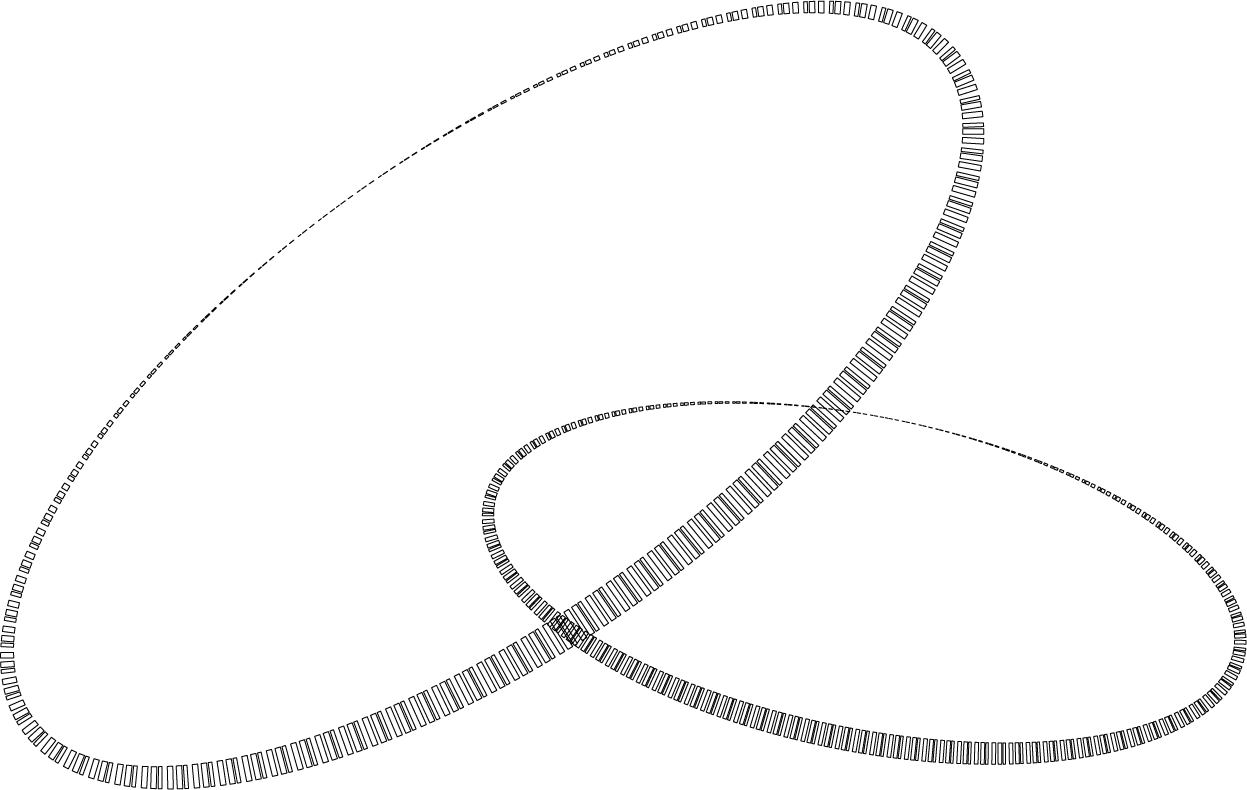
削ることが困難だった二段ギヤの小径部分も精密加工ができる
ギヤホーニングマシンを開発
ギヤホーニングマシンは、歯車加工の工程の中で、熱処理後に加工した歯車を砥石で研削する工作機械です。
歯車(ギヤ)は、エンジンやモーターの動力を働く力に変換するために使用される部品で、自動車や産業機械、航空機など用途も様々です。
そのため、工作機械には高精度な加工技術が求められています。
電動車両に求められる品質を落とすことなくユーザーのニーズに応えられる新しい工作機械、ギヤホーニング盤FX260の開発秘話を紹介します。
取材メンバー
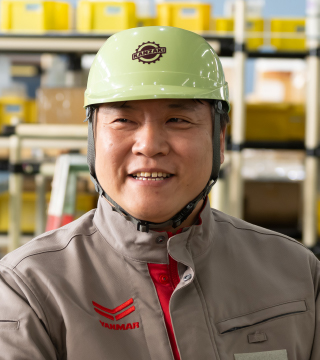
工作機械事業部
工機技術部 開発G
K.K.
2018年入社。
入社後2年間は工機生産部のサービス班にて、機械の試運転調整やお客様の工場での機械の立上げ・試運転をする業務に携わる。
2020年から工機技術部の営業G員となり、インド市場を中心にローカルの顧客や商社とコンタクトを取り、受注拡大を目指し活動中。
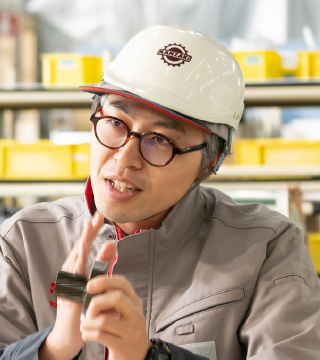
工作機械事業部
工機技術部 開発G
O.Y.
2013年入社。
大学院では機械工学専攻で自動車の振動騒音分析に関する研究に取り組む。
神崎入社後は商品設計部に配属されたのち開発Gに異動。
機械振動と加工精度に関する共同研究を母校と行い、FX260の開発においても共同で試験を実施。
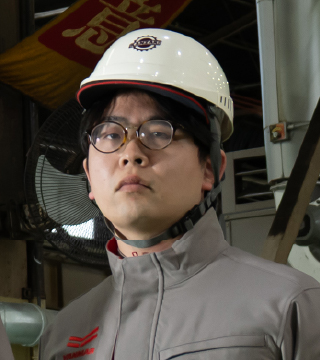
工作機械事業部
工機技術部 開発G
K.Y.
2016年入社。
高速同期ホーニング盤FF260や歯車研削盤GB260の開発・試験を担当。
トランスミッションメーカーへの出向経験を経て、現在はFF260のテストカットを通じ、多様な歯車加工に携わる。
工作機械見本市の目玉として開発がスタート
-
O.Y.さん -
2023年の夏、「JIMTOF2024(※)」で披露する目玉となる工作機械の開発プロジェクトが始動しました。
4年前に開発されたFF260の後継機を検討することは早い段階で決まっていましたが、商品コンセプトの決定には時間がかかりました。 -
K.K.さん -
私たち営業は、約2か月かけて60社以上の企業を訪問し、お客さまの声を徹底的にヒアリングしました。
その中で特に多かったのが、「生産性を向上させたい」「ランニングコストを抑えたい」「作業者のスキルによる品質のバラつきをなくしたい」といった要望でした。 -
K.Y.さん -
こうしたニーズをもとに、「生産性向上と品質の安定を実現できる機械」という方向でコンセプトを固めました。
とはいえ、生産性を高めるには、ギヤを研磨するヘッドの回転数を上げる必要があります。
しかし、回転数の増加に伴って振動や摩擦熱といった課題解決には、単なる設計変更では対応しきれませんでした。 -
O.Y.さん -
そこで、従来は鉄だったヘッドの素材を、ミネラルキャスティング(石材)に変更することを決断しました。
この素材は鉄に比べてギヤを研磨するときの振動が少なく、工具の摩耗を抑えられる点が魅力です。
ただし、当社ではこれまで使った実績がなく、まずは加工を引き受けてくれる業者を探すところから始める必要があり、非常に大変でした。 -
K.Y.さん -
さらに、ミネラルキャスティングは石材のため鉄よりも割れやすく、欠けやすいというデメリットもあります。
磁石が使えないなど、金属とは異なる特性もあり、従来機のFF260と性能を比較しながら、品質や操作性など一つひとつ検証していきました。 -
O.Y.さん -
効果を確かめるため、私の母校の大学と共同で試験を実施し、従来機との違いを詳細に分析しました。
また、ヘッドの耐久性試験も行いました。
設定した目標の耐久性を実現できたときは、「これなら製品化できる」と安堵したのを覚えています。
(※)日本国際工作機械見本市(Japan International Machine Tool Fair)。日本で開催される工作機械およびその関連機器等の展示会。
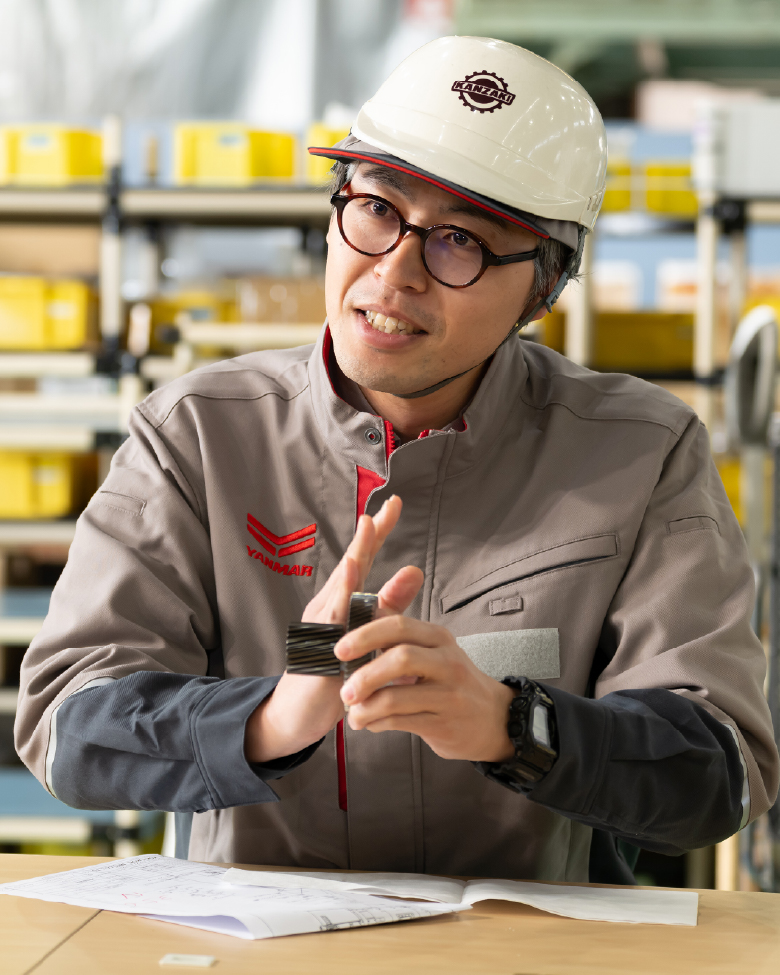
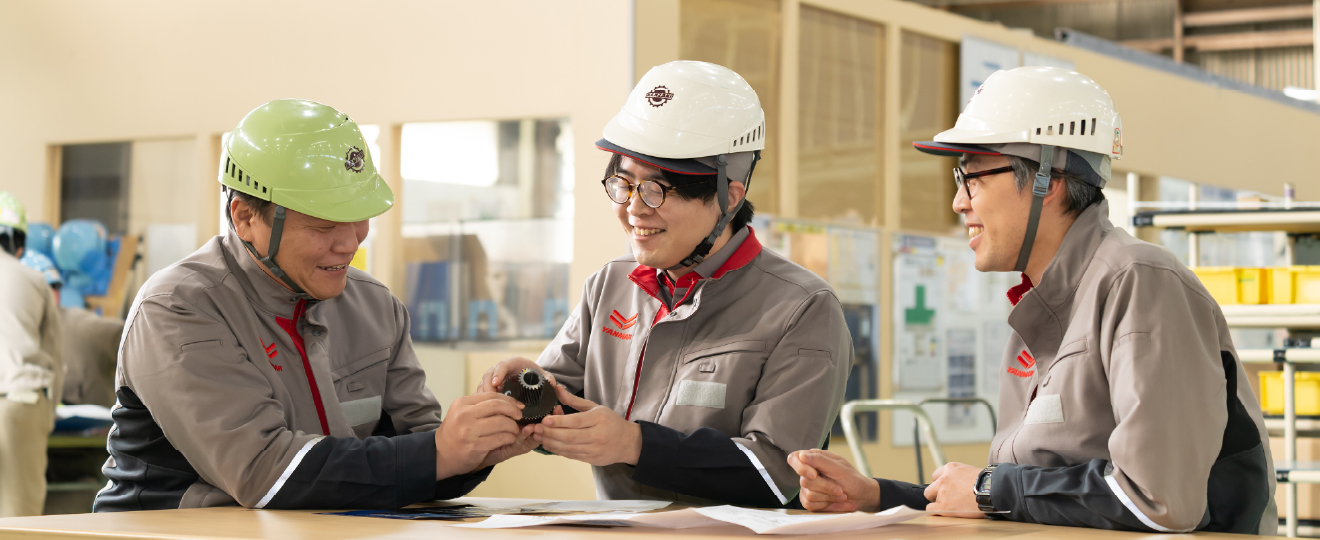
品質、コスト、デザインを徹底したからこそ、
自信の持てる製品に
-
K.K.さん -
ユーザーからは「見た目も大切」との声があり、今回はあえて“KANZAKIらしくない”カバーデザインに挑戦しました。
-
O.Y.さん -
デザインはヤンマーグループ内の協力を得て、ヤンマーのデザイン部と何度も協議を重ねながら決定しました。
小さな突起も見えないように隠すなど、スッキリとしたシャープな印象に仕上げています。
その結果、自信を持って「評判の良いデザイン」と言えるものが完成しました。 -
K.K.さん - 素材やデザインにこだわったことで、通常ならコストアップは避けられません。
しかし営業からは「価格は据え置きで」と要望しました。 -
K.Y.さん -
そこで開発では、ミネラルキャスティングを成形する際の加工工程を見直しするなど、細部までコストダウンの工夫を凝らしました。
-
K.K.さん -
その成果もあり、JIMTOF2024では多くのお客さまにFX260の革新性をご理解いただき、目標としていた1件の成約も達成しました。
現在も大きな反響が続いており、FX260が次世代のギヤ加工の主役になると確信しています。
開発を終えて感じるのですが、商品を開発することは大変なことも多いですが、大きな達成感を得られてやりがいもありますね。 -
K.Y.さん -
私は開発を通して、機械設計の難しさを改めて実感しました。
FX260は、機能を重視するあまり、組み立て工程を二の次にしてしまいました。
若干組み立てが複雑で完成までに時間がかかってしまいます。
今後は、品質とともに組み立てやすい設計も意識したいと思います。 -
K.K.さん -
私も、お客さまのニーズに日頃からアンテナを張っておく重要性を再認識しました。
「自動化したい」という要望の背景には「人材不足」という課題があるように、声の奥にある真のニーズを汲み取る力が求められます。
今後も「なぜそれが必要なのか」を含めて、開発にしっかりとバトンを渡していきたいですね。 -
O.Y.さん - 営業からの情報を待つだけでなく、私たちからも積極的にニーズを発信できるようになりたいです。
視野を広げ、関わるすべての人が納得できる“より良いものづくり”を目指していきます。
今後のKANZAKIの工作機械の進化にも、ぜひご期待ください。
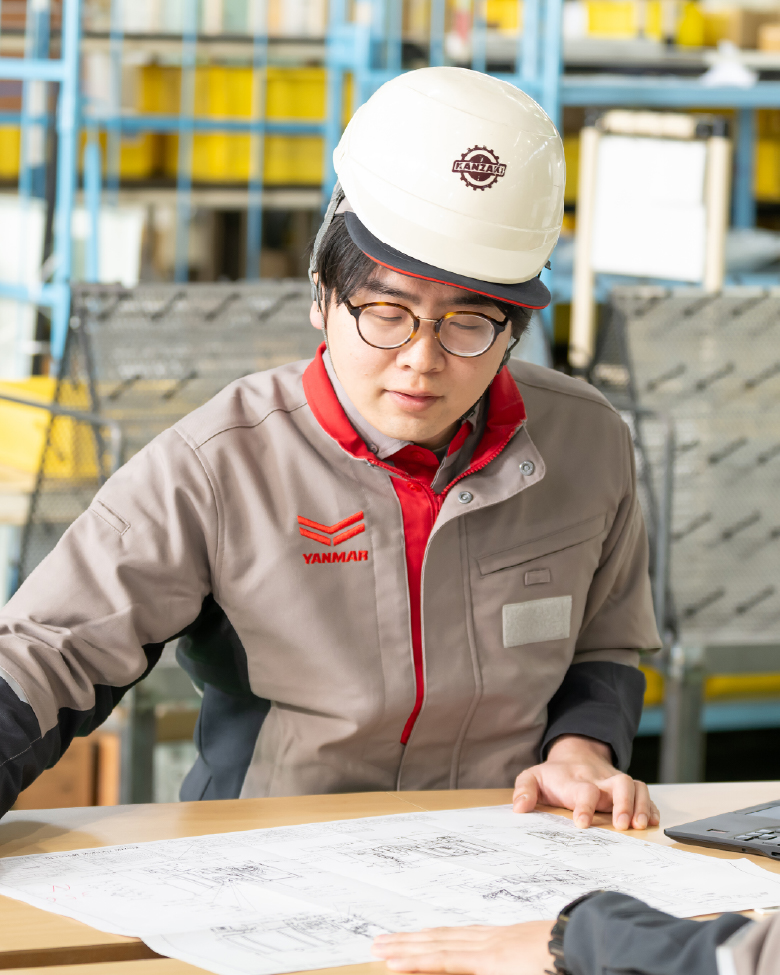
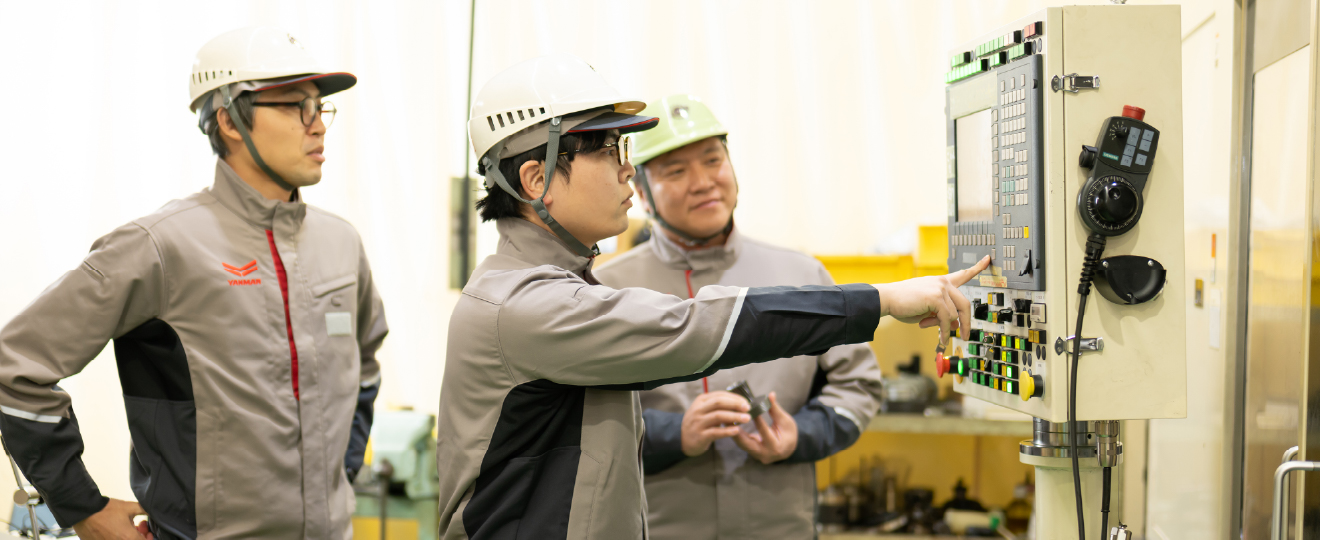
Another Story