- Home
- [Work] Project Story
- Development and design of an assembly and test run line for lawn mower transmissions for TTC (TUFF TORQ CORPORATION)
Project Story.05 Project Story
For TTC (TUFF TORQ CORPORATION)
For lawn mowers
Transmission assembly
Development and design of trial operation line
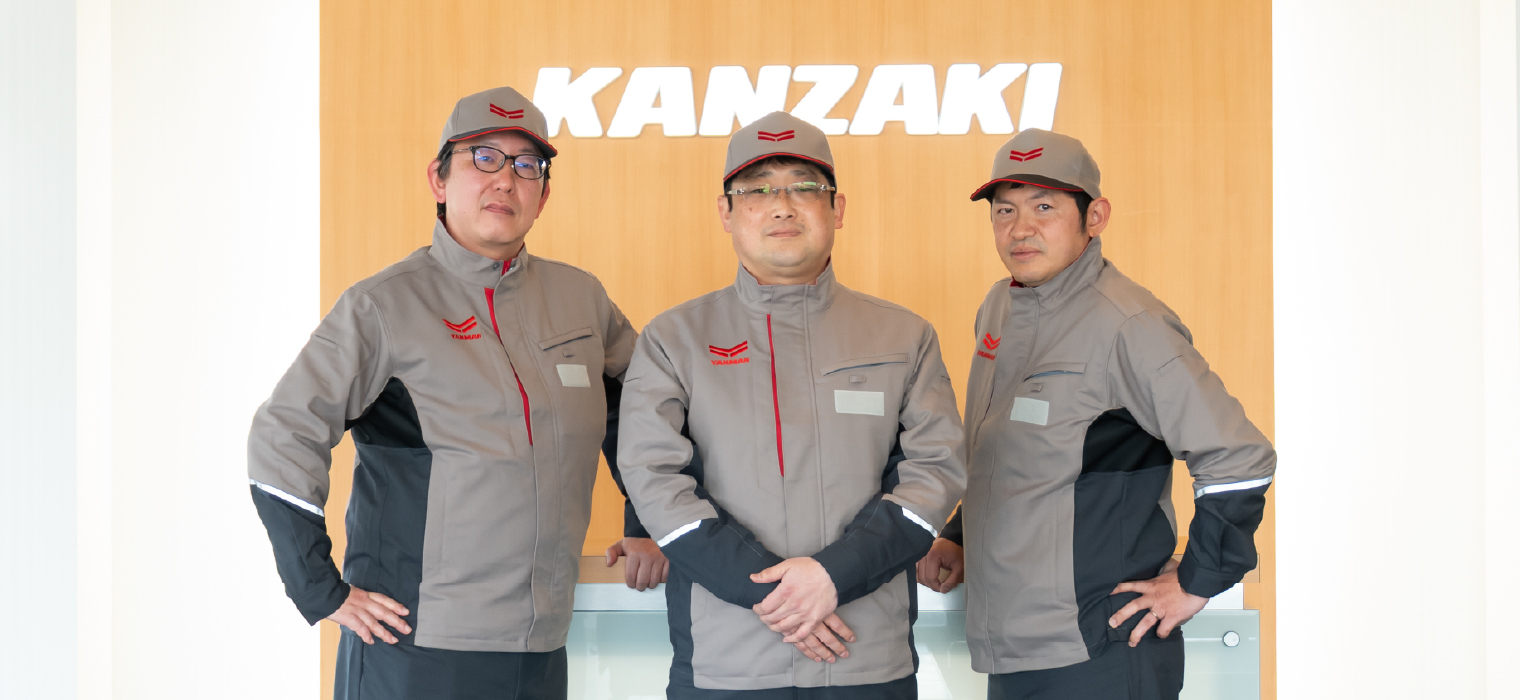
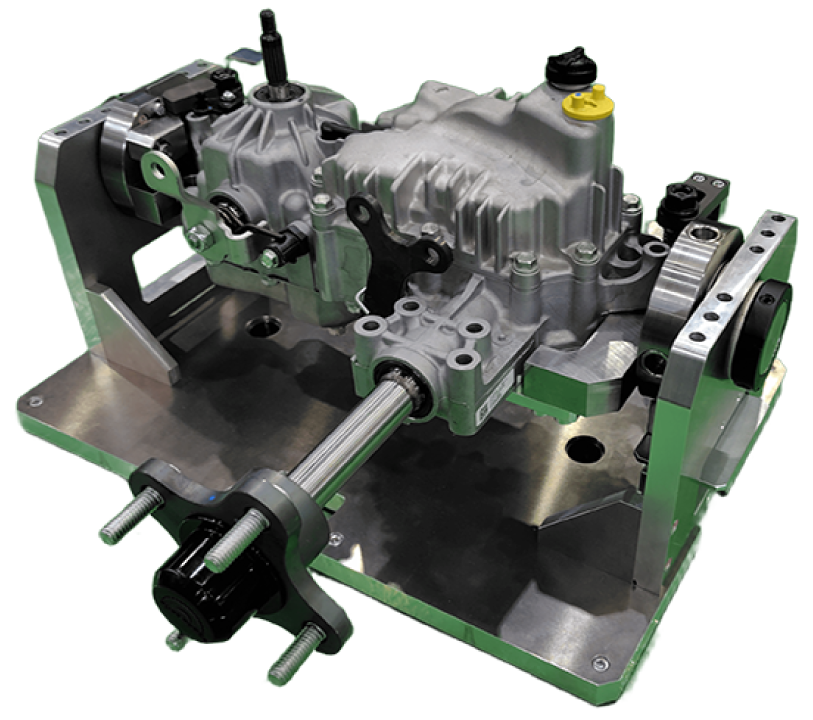
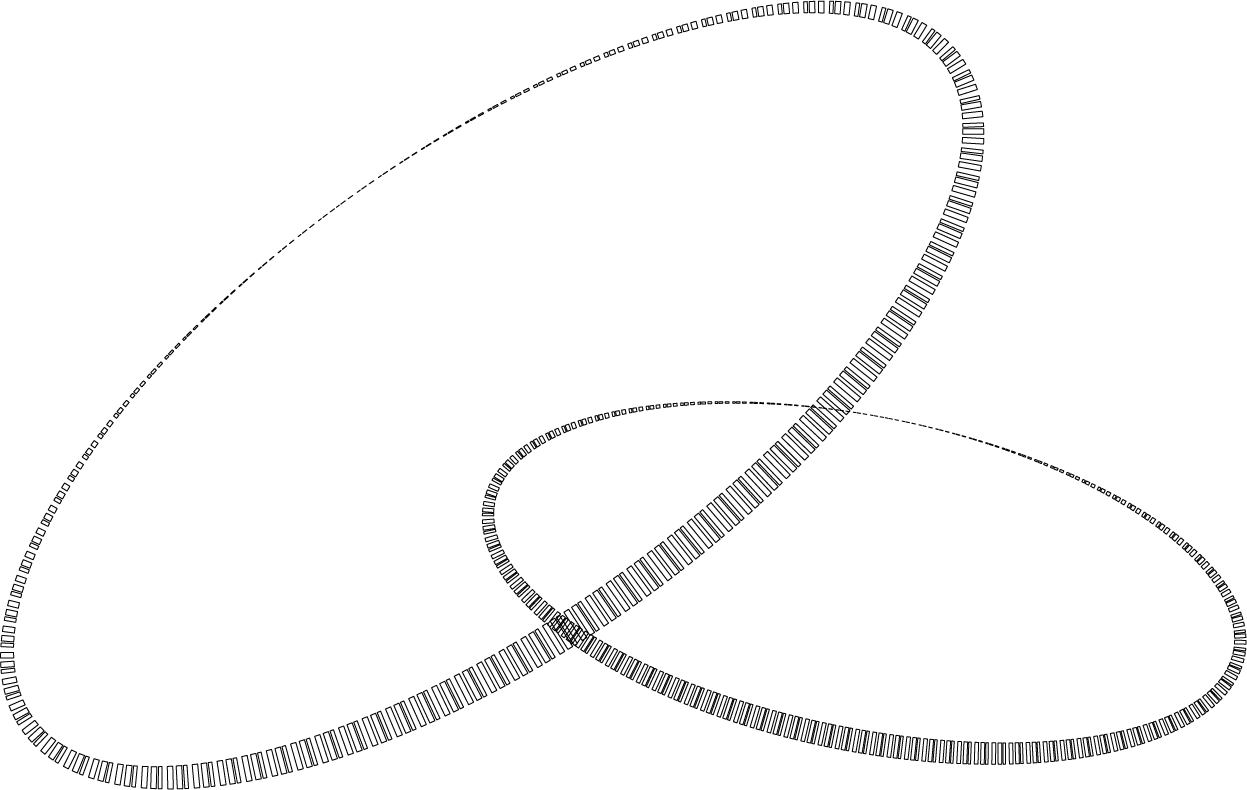
The production line is over 50m long!
Achieving automation of the transmission test run process
Due to a reduction in manufacturing personnel and the need to improve operational efficiency, an increasing number of companies are adopting production processes that do not involve human intervention, such as the rapidly evolving IoT and robotics at manufacturing sites.
Since we are automating work that has traditionally been done by people, there are considerable challenges in taking that first step and making it a reality.
The development of an assembly and test run line for lawnmower transmissions introduced here is an example of a solution we undertook to solve a customer's problem of wanting to automate the test run process (oil supply, air bleeding, neutral adjustment, test run) which had previously been performed by manual adjustment and changeover, thereby resolving labor shortages and achieving stable quality.
What's more, the production line is over 50 meters long!
Our challenge began with a discussion about what we wanted to automate and how much we could achieve.
Interview members
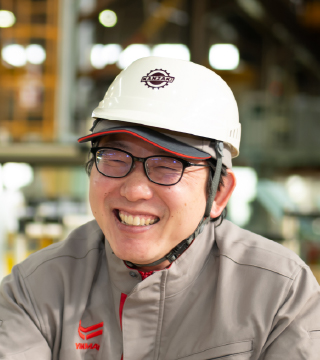
Machine tool division
Machinery Technology Department, Development Group
IY
Joined the company in 2015.
He majored in mechanical engineering at university.
He has an interest in the world of manufacturing and has many years of experience in machine design using 3D-CAD in the machine tool industry.
His current main job is in charge of mechanical design of vertical lathes and special-purpose machines.
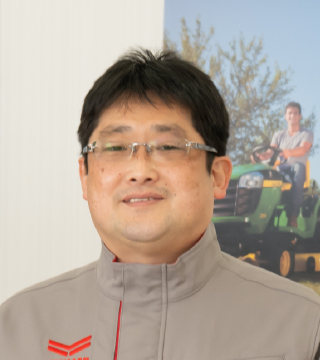
Machine tool division
Machinery Technology Department, Development Group
TT
Joined the company in 2013.
She is currently struggling to balance work and raising seven children.
His current main job is designing the control panels and operation panels for machine tools, and writing the ladder programs used to control the machine tools.
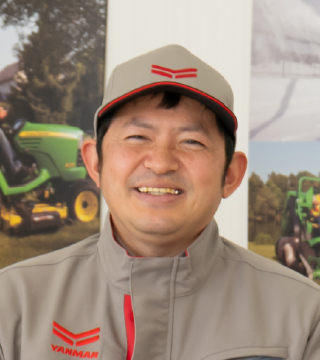
Machine tool division
Machinery Production Department Machinery Production Section
NM
Joined the company in 2016.
Originally from the main island of Okinawa, she loves the blue sea, coral, and awamori.
His current main job is to start up and test run special-purpose machines, and to act as a service engineer after machines are shipped domestically and overseas.
As I travel abroad often for work, I can provide you with all kinds of information about local food in various countries.
Starting the design almost from scratch
-
IYMr. Miss. -
The project to develop a lawnmower transmission assembly and test run line for TTC was first discussed around September 2020, and full-scale progress began around the beginning of 2021.
We received a direct message from TTC, our US subsidiary, that they needed a new line.
The background to this seems to be that demand for lawn mowers has been increasing year by year, and current production capacity is not enough to meet the demand. -
TTMr. Miss. -
The biggest challenge was automating the neutral adjustment process, which had long been done by hand by craftsmen.
Additionally, the line had to be stopped and the setup changed manually depending on the model being assembled, but there was a request to automate this as well.
This was expected to improve production efficiency and stabilize quality. -
NMMr. Miss. -
As expected, it was difficult to replace the fine-tuning work that had previously been done by hand with machines.
It took three months of trial and error to fully automate the process, which previously involved moving a lever on the product to check its rotation and then manually tightening the screws. -
IYMr. Miss. -
Although we had delivered about four similar lines in the past, more than 10 years had passed since the last project, and almost no one with the experience from back then remained.
Although we had previous drawings, we used them as a reference and adapted them to the customer's new requests, so we were practically starting the design from scratch. -
TTMr. Miss. -
During the project, there were times when it was difficult to procure parts due to the lockdown caused by the COVID-19 pandemic.
There were many times when we found ourselves unable to obtain the parts we had designed.
Each time we had to contact the entire Yanmar Group to find an alternative part or redesign the product, which was extremely difficult. -
IYMr. Miss. -
On a normal line, after the design is complete, the parts are gathered and assembled in order from largest to smallest, but this was not possible this time due to difficulties in procuring the parts.
Also, there were many times during assembly when I would realize, "Oh no, that's not right," and it was a constant process of trial and error. -
NMMr. Miss. -
Since the delivery destination was America, the line had to be divided and transported by ship, then reconnected at the destination. However, there were many parts, so it was difficult to assemble the conveyor accurately to ensure it was level and straight.
We also had an issue with the chains rusting during transportation, and during the test run, we had difficulty identifying where the problem was occurring, as the entire line, which is over 50 meters long, moves in tandem. -
TTMr. Miss. -
Controlling a massive line that is over 50m long is a truly enormous challenge.
A change in one place could affect the entire line, so we always had to know what was moving and where.
We stationed several people next to the line to monitor the work as it proceeded.
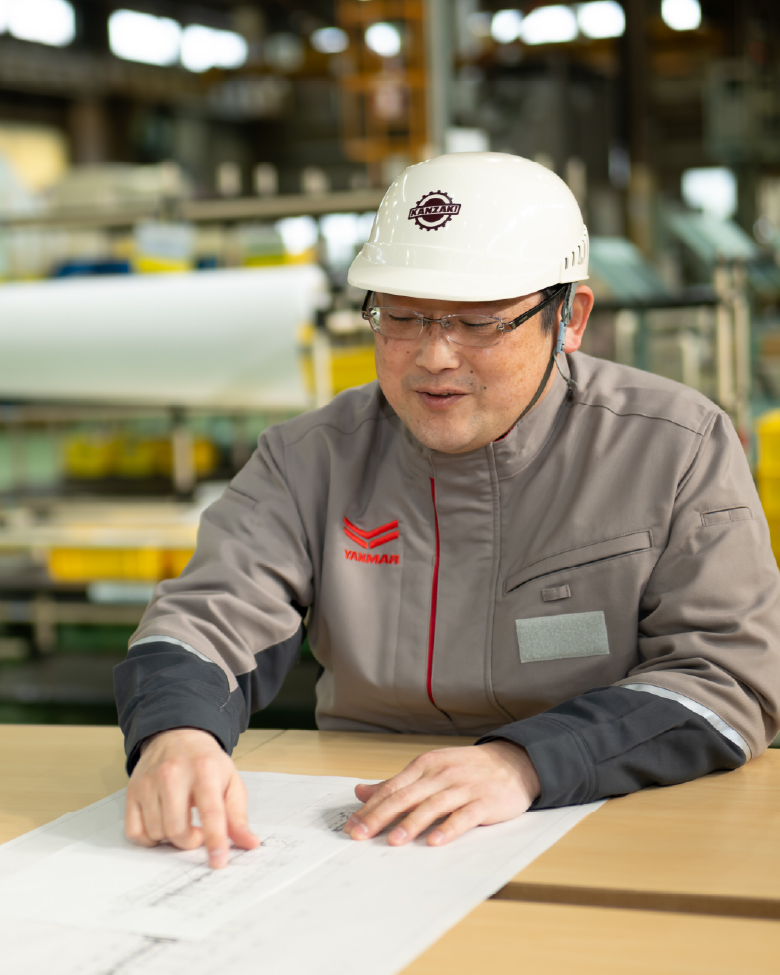
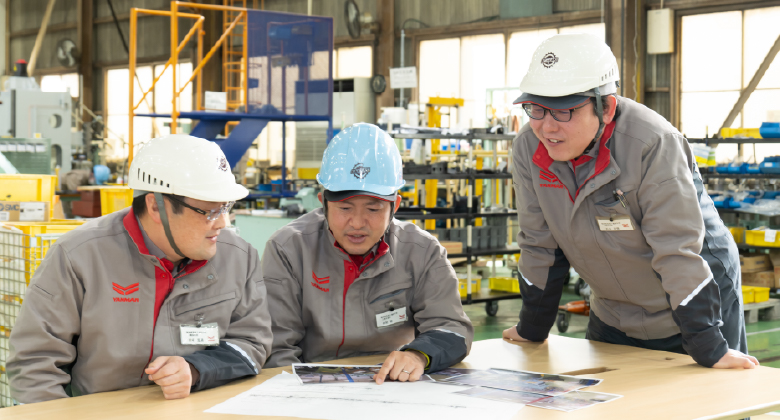
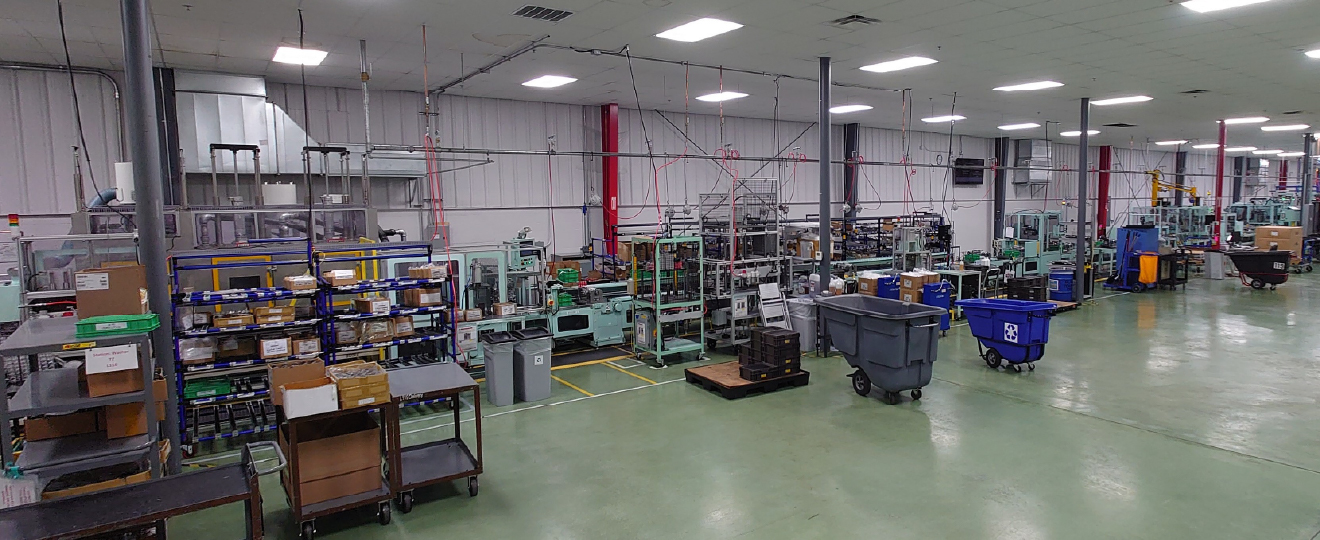
Overcoming difficulties through outstanding teamwork
-
NMMr. Miss. -
It was teamwork that enabled us to overcome so many of these difficulties.
This is because members of the design, procurement, and production teams came together, pooling their knowledge and experience, and working together to solve the problem. -
TTMr. Miss. -
Close communication with customers was also extremely important.
We held numerous conference calls from the early stages of development to thoroughly understand the purpose and details of the specification changes. -
IYMr. Miss. -
By proactively incorporating improvements made to the previous line and customer requests, we have been able to significantly improve customer satisfaction.
As a result, we have already received orders for the next line. -
TTMr. Miss. -
This project was extremely difficult, but by working together with other departments, I improved my communication skills and gained confidence that I can get my point across to overseas customers if I want to.
-
NMMr. Miss. -
I felt more determined to see it through to the end.
I was really impressed when the line actually started moving. -
IYMr. Miss. -
As a designer, I was reminded of the importance of listening to the voices of those on the front lines and creating feasible designs.
I also believe that I have improved my communication skills, which allows me to express in words what cannot be expressed through drawings alone.
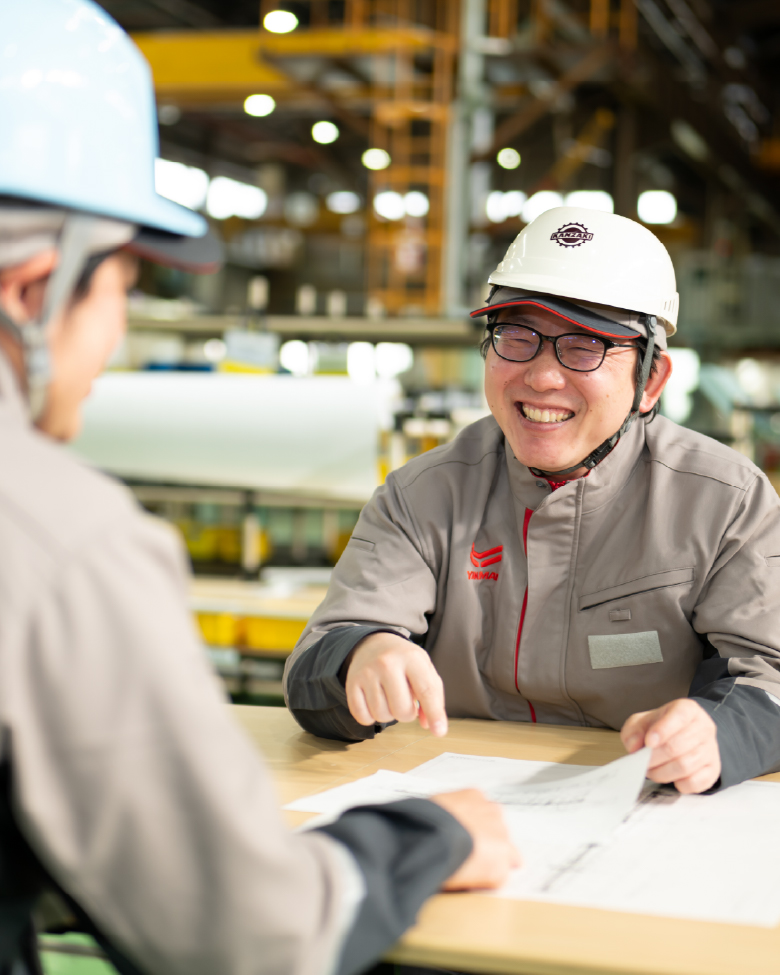
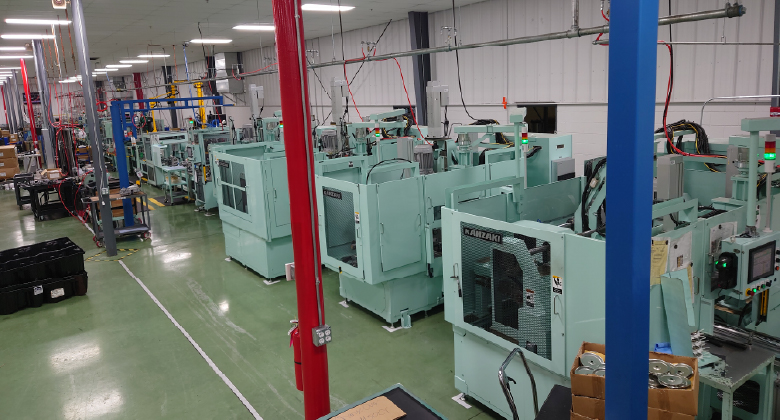
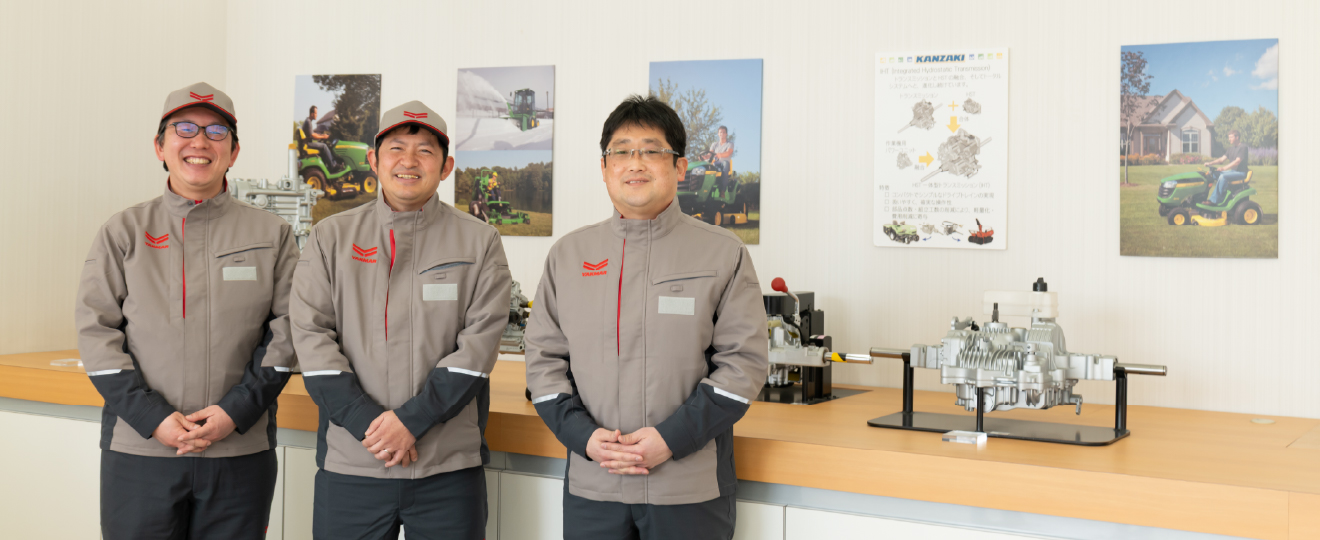
Another Story