- Home
- [Work] Project Story
- Developed a gear honing machine that improves productivity and stabilizes quality Gear Honing Machine FX260
Project Story.04 Project Story
Achieve improved productivity and stable quality
Gear honing machine developed
Gear Honing Machine FX260
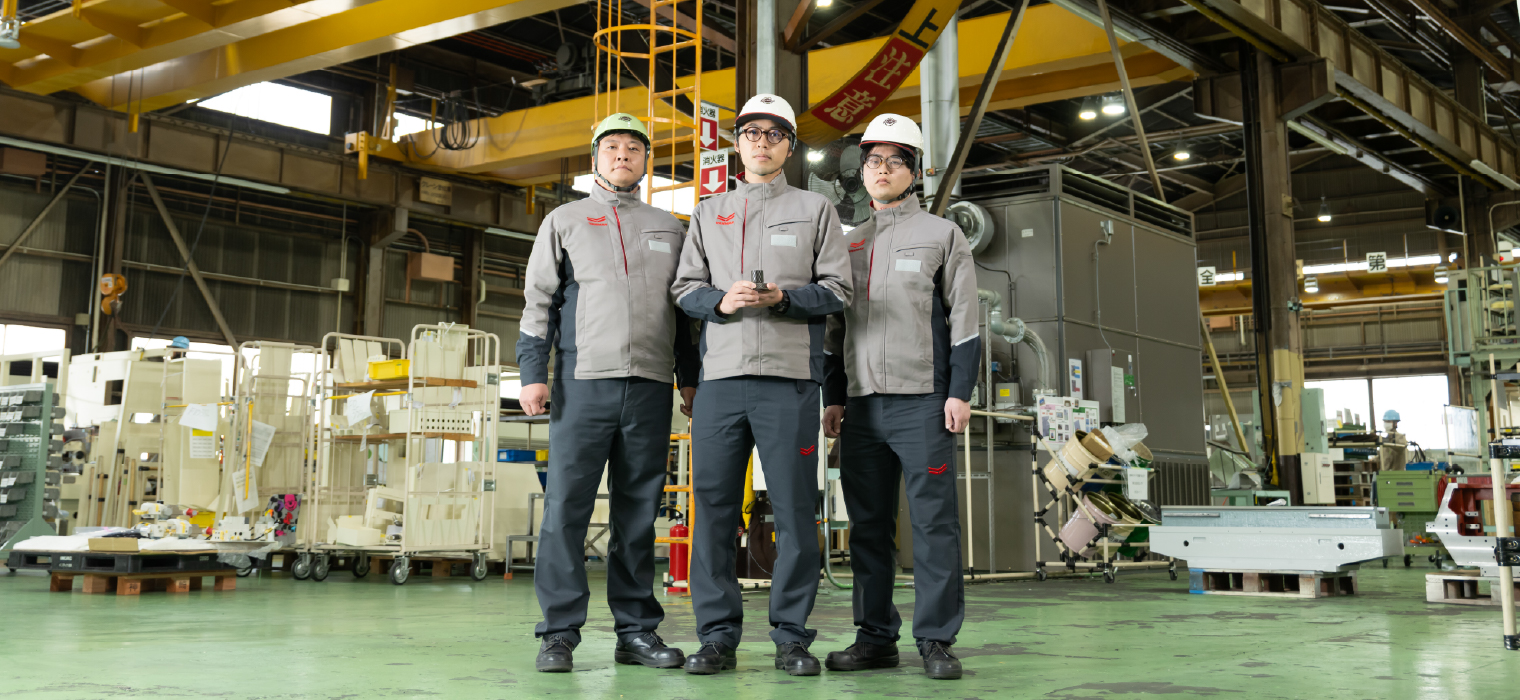
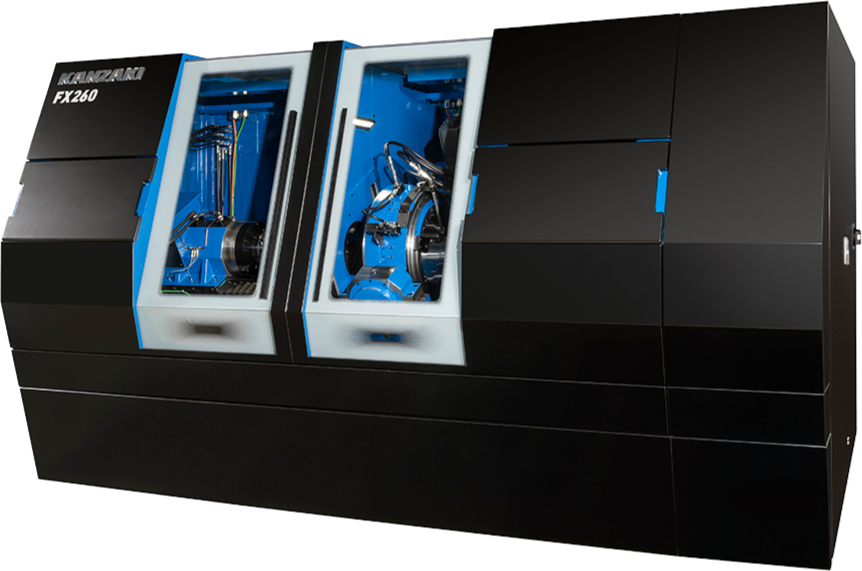
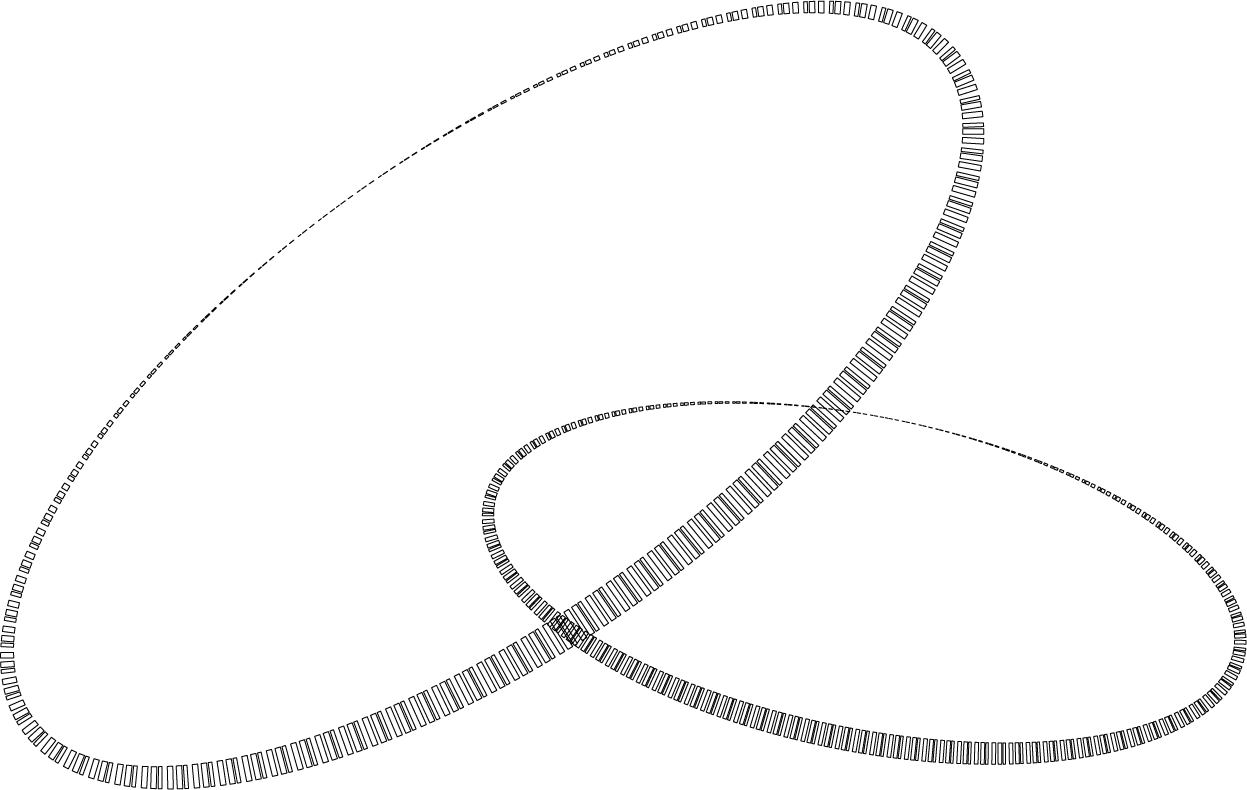
The small diameter parts of double gears, which were previously difficult to machine, can now be precisely machined.
Gear honing machine developed
A gear honing machine is a machine tool that uses a grinding wheel to grind gears that have been processed after heat treatment during the gear manufacturing process.
Gears are components used to convert the power of engines or motors into working force, and are used in a variety of applications, including automobiles, industrial machinery, and aircraft.
This requires machine tools to have high-precision machining technology.
We will introduce the story behind the development of the FX260 gear honing machine, a new machine tool that meets user needs without compromising the quality required for electric vehicles.
Interview members
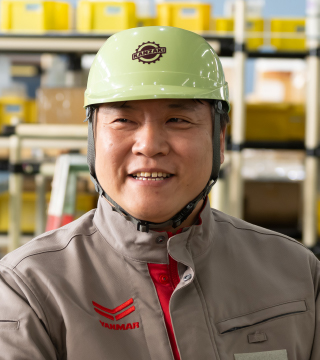
Machine tool division
Machinery Technology Department, Development Group
K.K.
Joined the company in 2018.
For the first two years after joining the company, I worked in the service team of the Machinery Production Department, where I was involved in test-running and adjusting machines, as well as setting up and test-running machines at customer factories.
Since 2020, he has been working as a sales representative in the Machinery and Technology Department, contacting local customers and trading companies, mainly in the Indian market, with the aim of expanding orders.
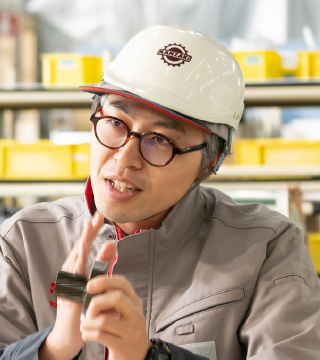
Machine tool division
Machinery Technology Department, Development Group
OY
Joined the company in 2013.
In graduate school, he majored in mechanical engineering and conducted research on automobile vibration and noise analysis.
After joining the company, Kanzaki was assigned to the Product Design Department and then transferred to the Development Group.
He conducted joint research with his alma mater on machine vibration and machining accuracy, and also conducted joint testing in the development of the FX260.
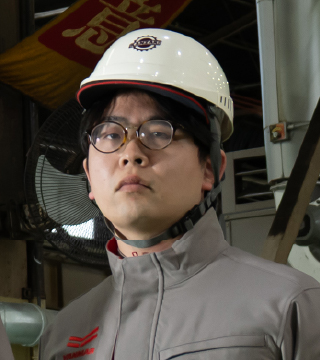
Machine tool division
Machinery Technology Department, Development Group
KY
Joined the company in 2016.
Responsible for the development and testing of the FF260 high-speed synchronous honing machine and the GB260 gear grinding machine.
After gaining experience working at a transmission manufacturer, he is now involved in a variety of gear processing, including test cutting of the FF260.
Development started as a highlight of the machine tool trade fair
-
OYMr. Miss. -
A development project has begun for the machine tool that will be the highlight of the exhibition at JIMTOF2024 (※) in the summer of 2023.
The decision to consider a successor to the FF260, which was developed four years ago, was made at an early stage, but it took time to decide on the product concept. -
K.K.Mr. Miss. -
Our sales team spent about two months visiting over 60 companies and thoroughly listening to customer feedback.
Among these, the most common requests were "We want to improve productivity," "We want to reduce running costs," and "We want to eliminate quality variations due to worker skill." -
KYMr. Miss. -
Based on these needs, we solidified the concept of creating a machine that can improve productivity and stabilize quality.
However, to increase productivity, the gear grinding head needs to rotate at a higher speed.
However, issues such as vibration and frictional heat that arise as the rotation speed increases cannot be resolved by simply changing the design. -
OYMr. Miss. -
Therefore, we decided to change the head material from iron to mineral casting (stone).
The appeal of this material is that it generates less vibration when grinding gears compared to iron, which helps reduce tool wear.
However, our company had no prior experience using this material, so we first had to find a company that would undertake the processing, which was extremely difficult. -
KYMr. Miss. -
Another disadvantage of mineral casting is that it is made of stone and is therefore more prone to cracking and chipping than steel.
It has characteristics that differ from metals, such as the inability to use magnets, so we compared its performance with the previous model, the FF260, and verified its quality, operability, and other aspects one by one. -
OYMr. Miss. -
To verify its effectiveness, I conducted tests in collaboration with my alma mater and conducted a detailed analysis of the differences between this machine and conventional machines.
We also conducted durability tests on the heads.
I remember feeling relieved when we achieved the durability target we had set, thinking, "Now we can put this into production."
(※) Japan International Machine Tool Fair: An exhibition of machine tools and related equipment held in Japan.
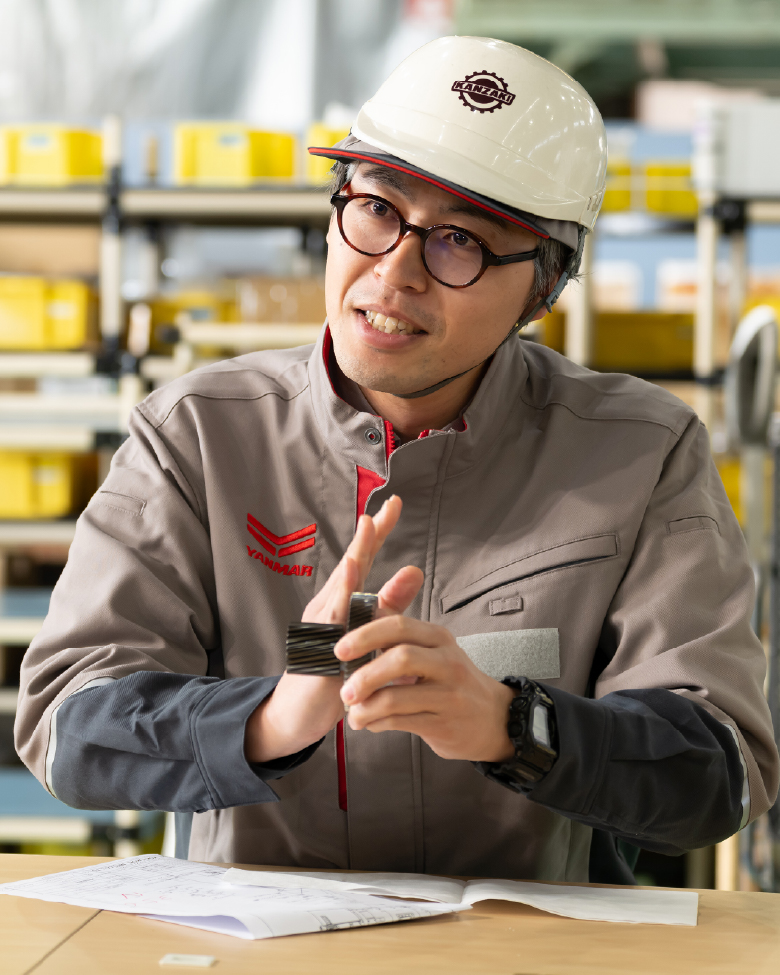
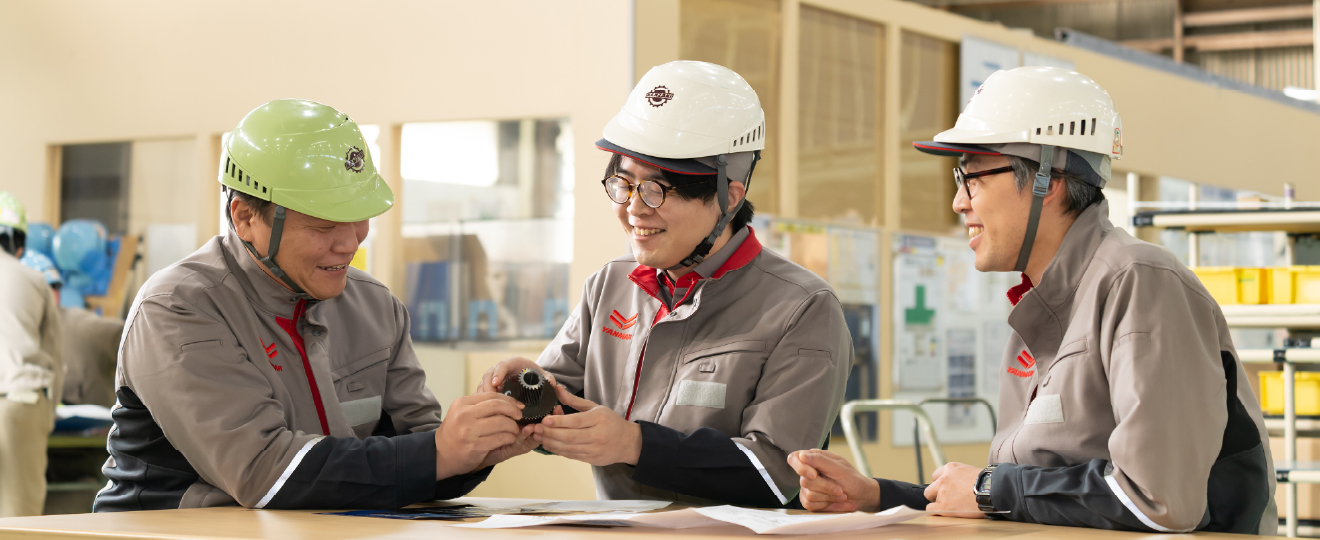
With a thorough focus on quality, cost and design,
A product you can be confident in
-
K.K.Mr. Miss. -
Users have commented that "appearance is also important," so this time we deliberately tried to create a cover design that was "un-KANZAKI-like."
-
OYMr. Miss. -
The design was decided upon after numerous discussions with Yanmar's Design Department, with cooperation from within the Yanmar Group.
Even the small protrusions are hidden, giving it a clean, sharp impression.
The result is something we can confidently call a "well-received design." -
K.K.Mr. Miss. - Normally, focusing on materials and design would inevitably result in increased costs.
However, the sales department requested that the price remain the same. -
KYMr. Miss. -
So during development, we took great care to reduce costs down to the smallest details, including reviewing the processing steps for forming the mineral casting.
-
K.K.Mr. Miss. -
As a result, at JIMTOF2024, many customers understood the innovative nature of the FX260, and we achieved our goal of closing one deal.
The response is still overwhelming, and we are convinced that the FX260 will become a leader in the next generation of gear machining.
Now that we've completed development, I realize that developing a product can be difficult at times, but it's also rewarding because it gives you a great sense of accomplishment. -
KYMr. Miss. -
Through this development, I was reminded of just how difficult machine design is.
With the FX260, the emphasis is on functionality, so much so that the assembly process takes a back seat.
The assembly is somewhat complicated and takes some time to complete.
In the future, I would like to pay attention not only to quality but also to designs that are easy to assemble. -
K.K.Mr. Miss. -
I too was reminded of the importance of always keeping an eye on customer needs.
Just as the desire for automation is often accompanied by the issue of a shortage of human resources, the ability to discern the true needs behind these voices is essential.
I would like to continue to pass the baton to development, including considering "why this is necessary." -
OYMr. Miss. - Rather than just waiting for information from sales, we would like to be able to proactively communicate our needs.
We will broaden our horizons and aim to create better products that satisfy everyone involved.
Please look forward to the future evolution of KANZAKI's machine tools.
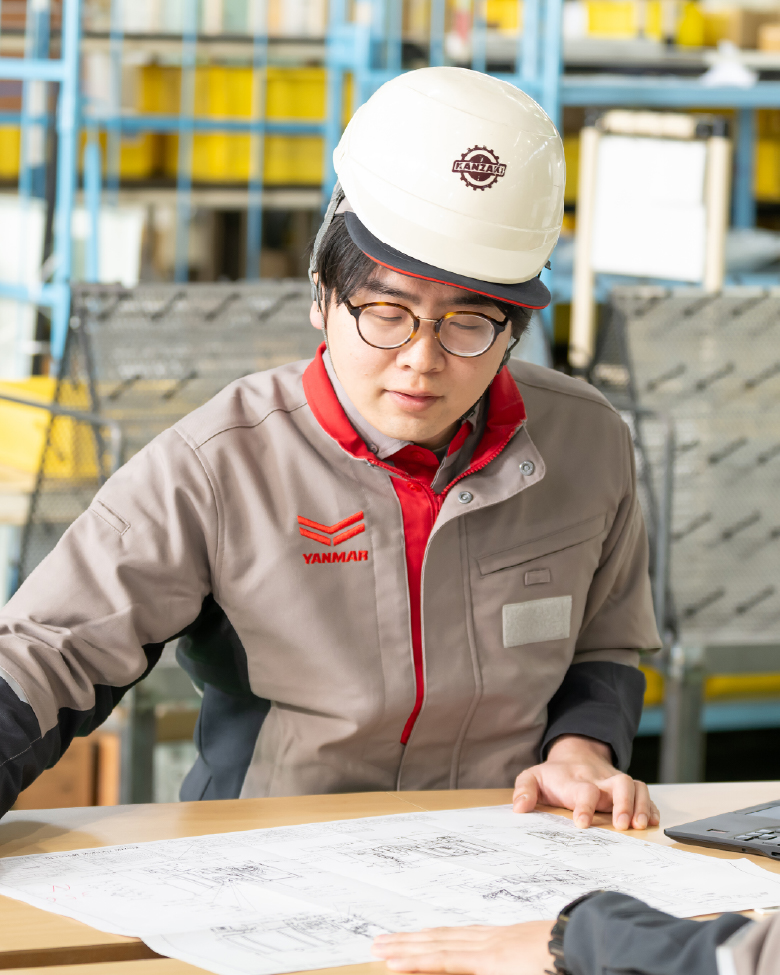
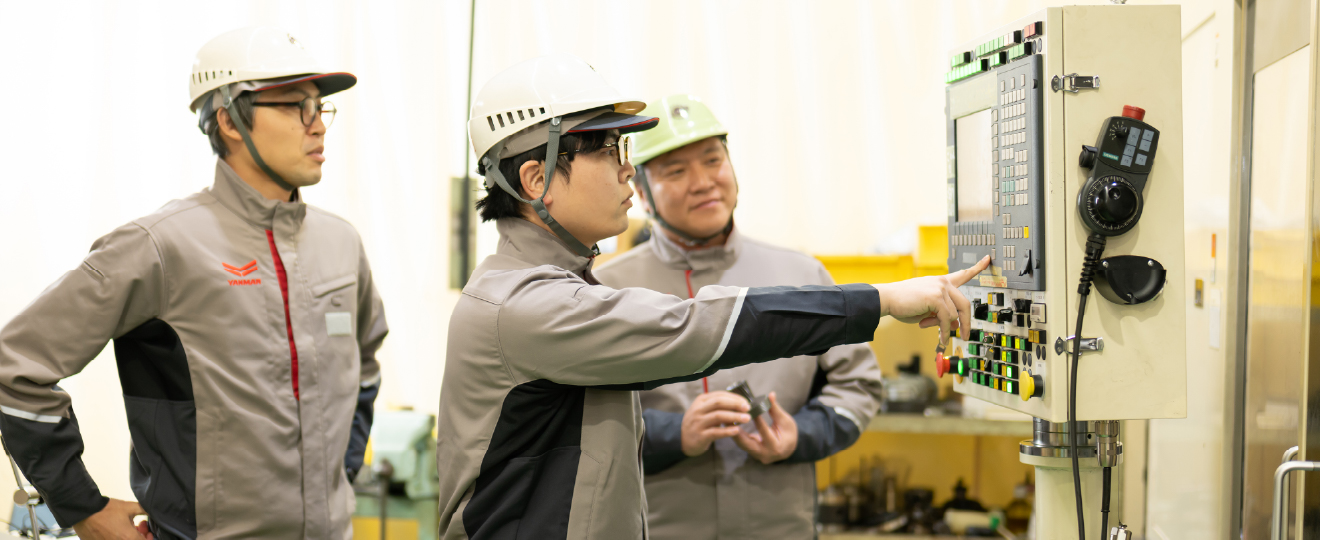
Another Story