- Home
- [Work] Project Story
- Hydraulic four-wheel drive development project HFWD (Hydraulic front axle for four-wheel drive)
Project Story.02 Project Story
Hydraulic four-wheel drive development project
HFWD
(Hydraulic four-wheel drive front axle)
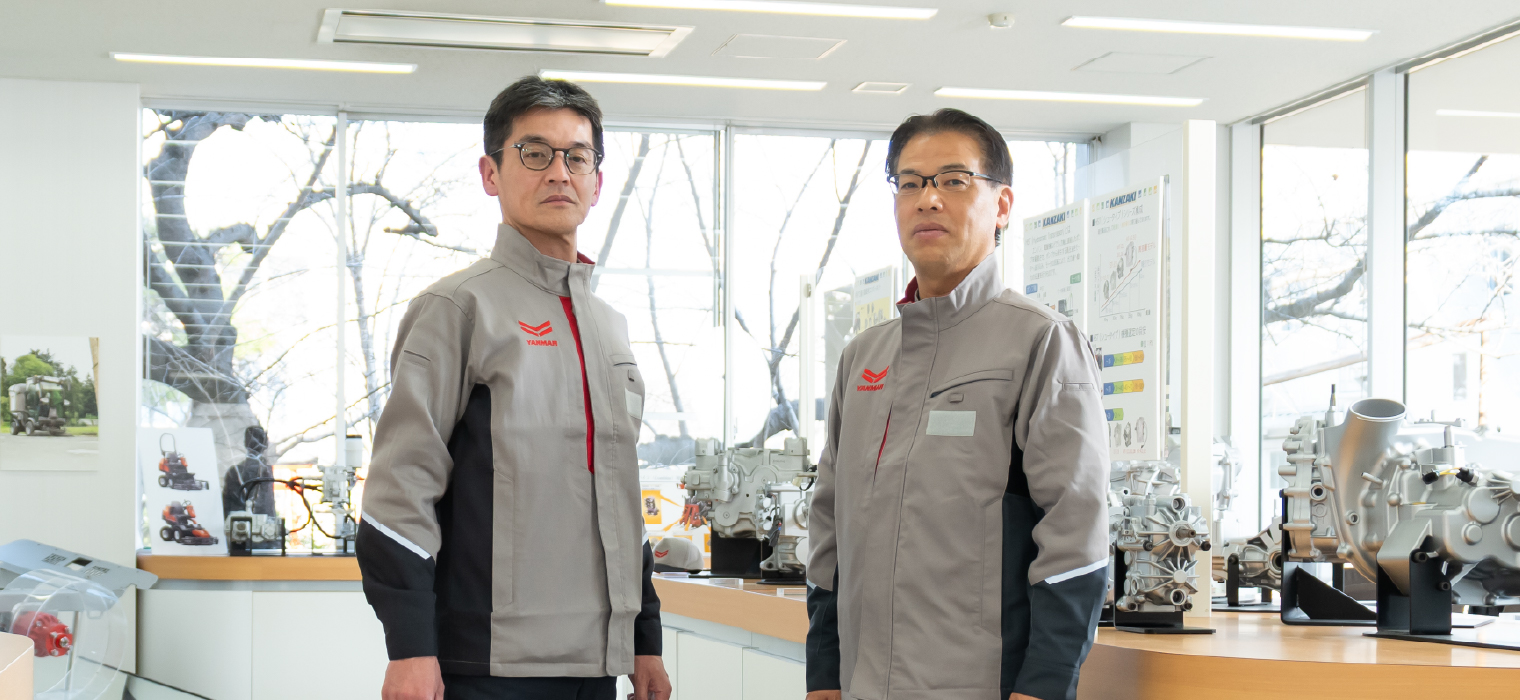
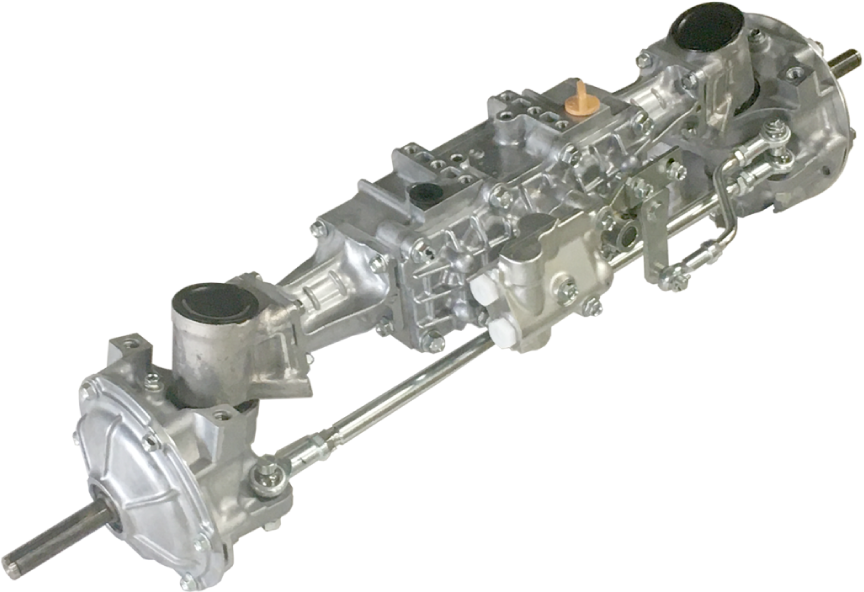
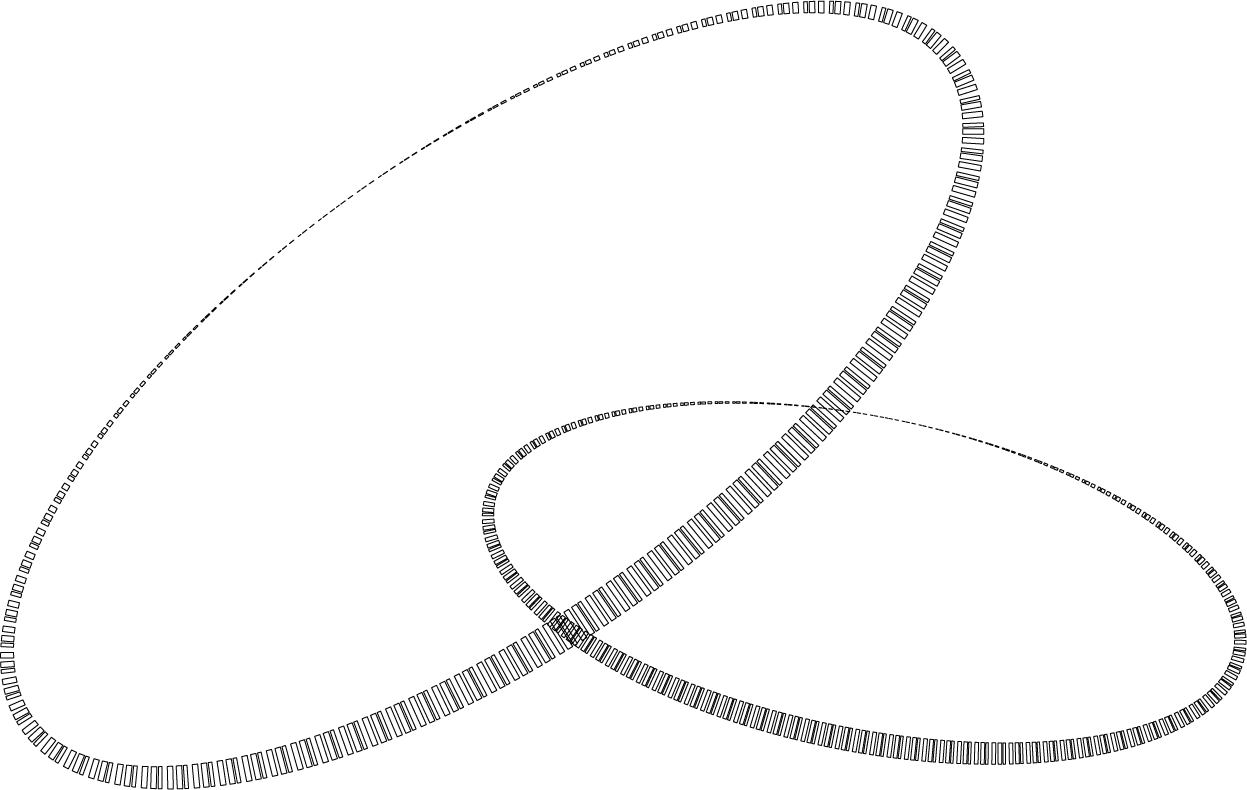
Utilizing Kanzaki's hydraulic and gear technologies
Unique products
When you think of 4WD vehicles, you probably imagine excellent driving performance and stability on rough roads.
Stable driving is achieved by connecting the front and rear of the vehicle with a driveshaft, transmitting power from the engine to all of the wheels.
In that case, many people may be thinking how great it would be to have a 4WD lawnmower, which can easily climb steep slopes that are not always flat.
However, with riding lawn mowers, the grass-cutting equipment is mounted underneath the body, so it's not such a simple issue.
In the midst of this, a project was launched to create a one-of-a-kind product by utilizing KANZAKI's strengths in hydraulic technology and gear technology.
He shared the inside story behind the development.
Interview members
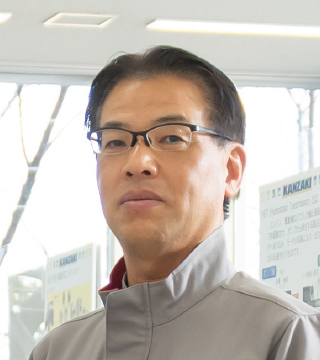
Development Department Product Development Department
Second product G
IK
Joined the company in 1991.
Since joining the company, he has been involved in development work and has experienced numerous development projects including lawn mowers, agricultural machinery, and utility vehicles.
He currently serves as the chair of the group's contribution activities.
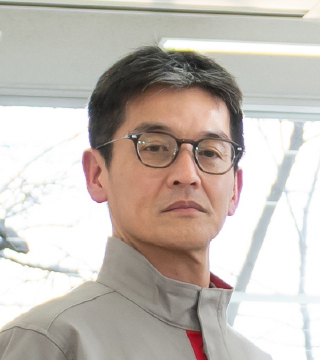
Development Department
Test G
HH
Joined the company in 1992.
Since joining the company, he has been involved in testing, experiencing testing work on a variety of development projects, including hydraulic transmissions (IHT) for lawnmowers.
Currently, he is still actively working alongside younger employees, focusing on testing transmissions for utility vehicles.
With the goal of creating new value
-
IKMr. Miss. -
This project started as a proposal-based product development initiative in which KANZAKI sought to utilize its strengths to create new, unique value.
-
HHMr. Miss. -
In conventional 4WD systems, the front and rear of the vehicle are typically connected by a drive shaft, but this inevitably gets in the way when the mower is raised and lowered to cut the grass.
As a result, 4WD lawn mowers were not widely available on the market.
So the idea was born to replace the drive shaft with a hydraulic one. -
IKMr. Miss. -
During development, weight reduction was the top priority.
In order to reduce weight, it is important to consider what material to use for the case.
The aluminum used in the first unit was not strong enough.
During the test, an issue occurred where the piece broke in half, causing some headaches. -
HHMr. Miss. -
From there it was a process of trial and error.
We meticulously measured the stress on the case, collected data, and repeatedly performed structural analysis.
After going through the process of making, breaking and improving multiple prototypes, we were finally able to create a case that would not break. -
IKMr. Miss. -
We considered changing the material, but we were determined to make it lighter as it will be used on grass, and decided to keep the aluminum material while increasing its strength through heat treatment.
-
HHMr. Miss. -
The hydraulic system also presented challenges.
With the first model we developed, the rotation speed of the front and rear wheels did not match the oil flow rate well, causing friction between the tires and making it difficult to drive smoothly.
To address this issue, a component called a check valve was added, which introduced a mechanism that allows oil to be replenished from the tank in response to discrepancies in the rotation speeds of the front and rear wheels, thereby solving the problem. -
IKMr. Miss. -
Even after the product was completed, problems arose during production.
The bevel gears used in HFWD were machined with a tool to cut the teeth during the prototype stage, but for mass production, this was changed to a method of forming them using a mold called forging. As a result, the metal did not reach the tip of the mold sufficiently during the manufacturing of the gears, resulting in rounded teeth.
This caused the gears to not mesh properly with the other gears, resulting in a loud noise.
To address this issue, we improved the forging method and adjusted it so that metal was filled all the way to the tips of the teeth, thereby reducing the noise.
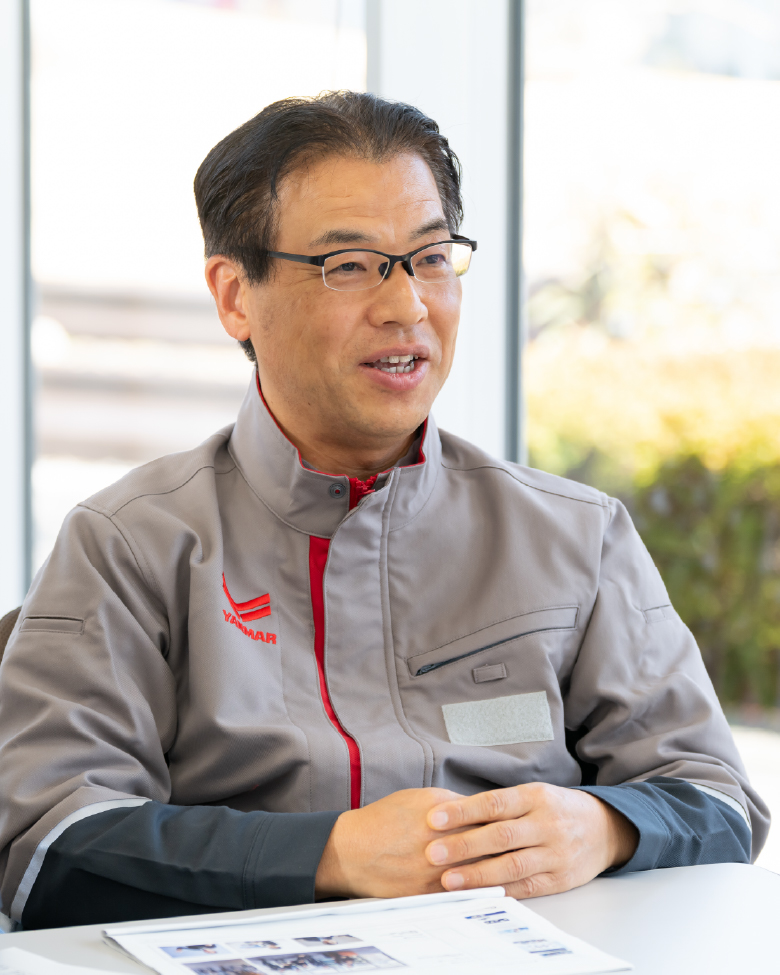
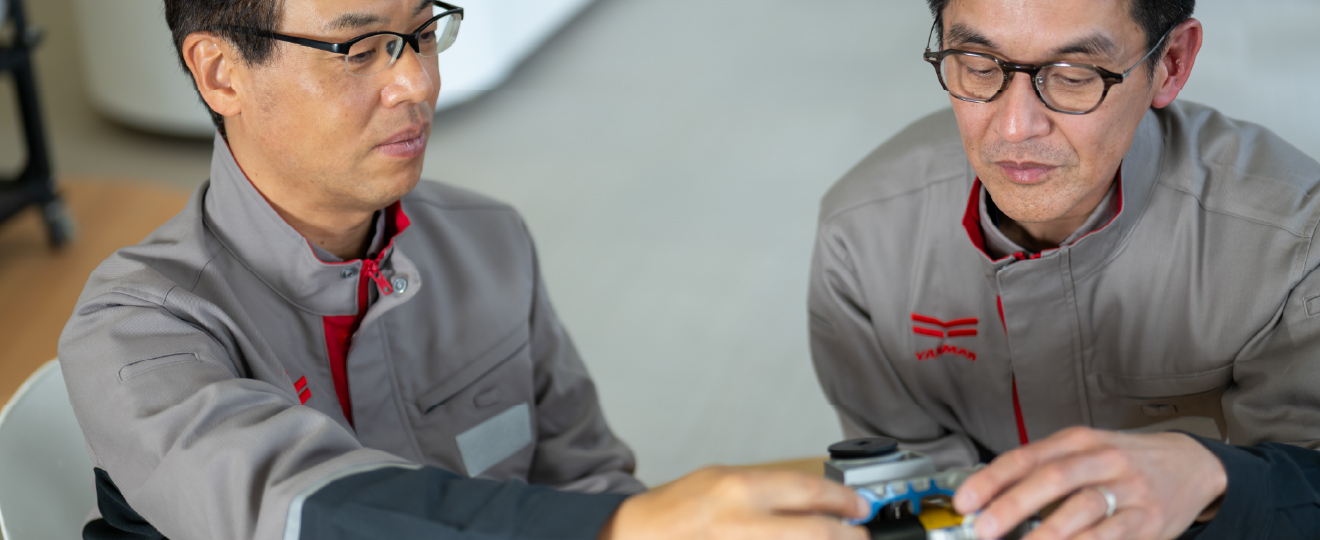
Product development through cooperation between various departments
-
HHMr. Miss. -
The HFWD development project was a first for Kanzaki, incorporating concurrent engineering techniques, with many departments working together to bring the product to market, including not only the Development and Materials departments but also the Sales, Production Technology and Accounting departments.
As part of the cost reduction activities, the sales department visited manufacturers to strongly communicate their sales targets and promise to increase production volume, while the production technology department worked with manufacturers to consider processes for reducing manufacturing costs. Each department made an effort to utilize their respective expertise. -
IKMr. Miss. - I feel that this project was successful precisely because of the strong desire to somehow commercialize the product and the active cooperation of all the relevant departments.
I realized that things that cannot be done alone can be achieved if more people share the same passion. -
HHMr. Miss. -
I am grateful that I was able to learn a lot about gears and hydraulics through the development of the HFWD, and that the trial and error tests I conducted under simulating harsh operating conditions helped me develop my critical thinking skills.
-
IKMr. Miss. - HFWD has been highly praised in the market for its excellent performance and has been widely adopted especially in European countries with many hilly areas, achieving success unmatched by its competitors.
-
HHMr. Miss. -
We received inquiries from domestic manufacturers, and when we demonstrated the high off-road capabilities of special lawnmowers (grass cutters) that are resistant to rough roads, such as those used in orchards, we felt that all the hard work during development had paid off, and we were very pleased.
HFWD is truly a product that culminates Kanzaki's technological capabilities and the enthusiasm of everyone involved.
The experience gained here has become a representative success story for KANZAKI as we continue to take on new challenges.
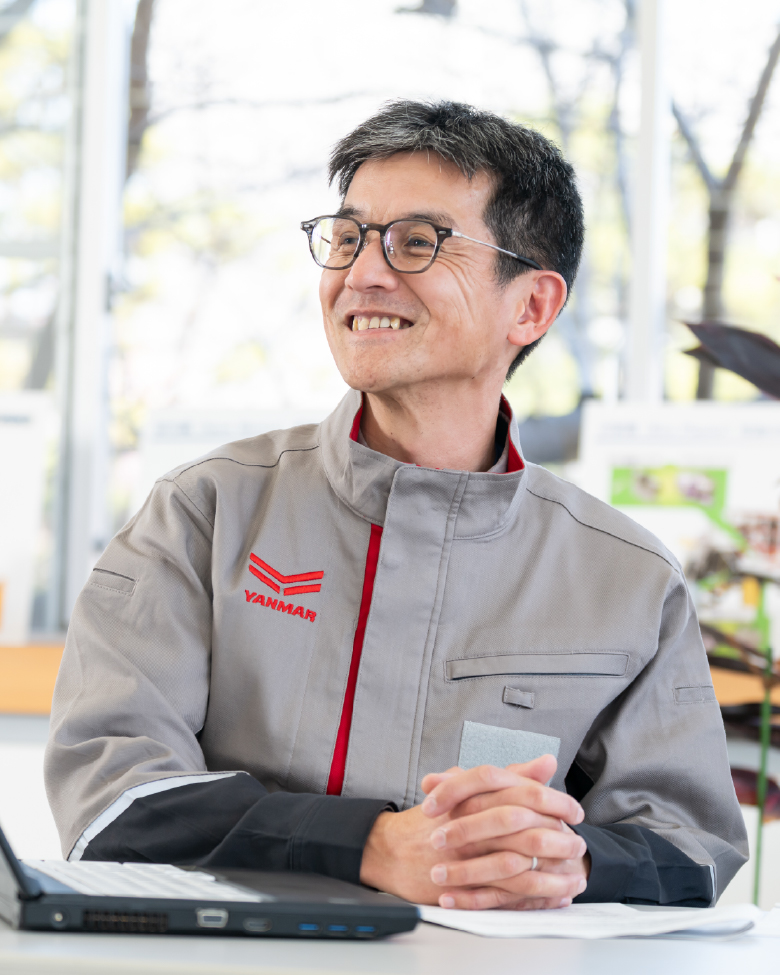
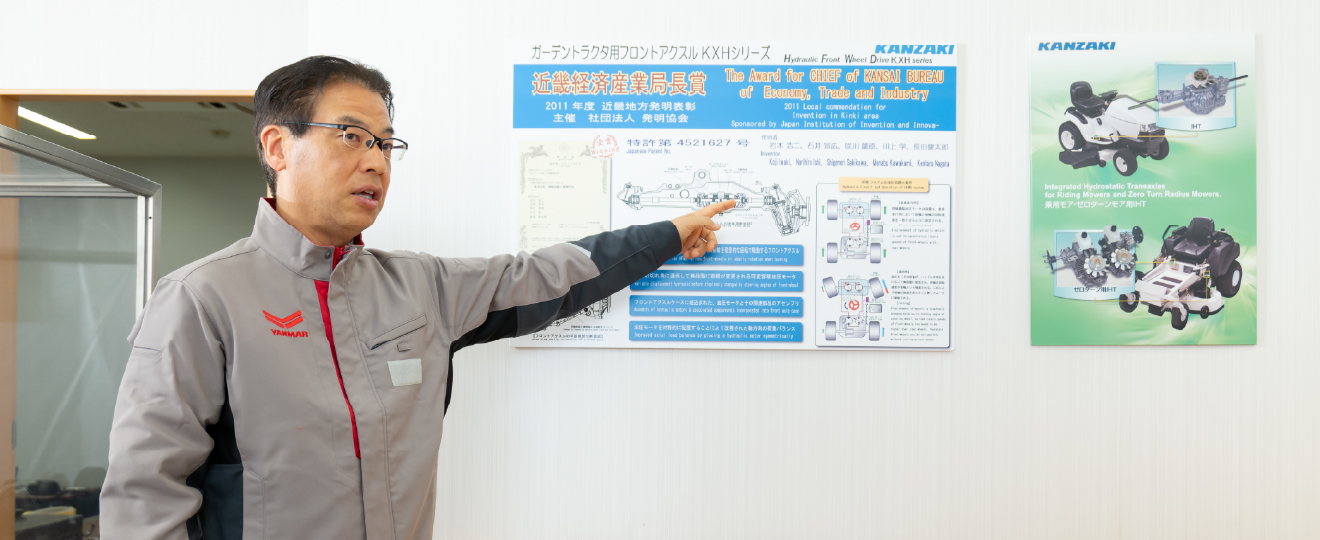
Another Story