- Home
- [Work] Project Story
- Electric riding lawn mower development project e-DS mower
Project Story.03 Project Story
Electric riding lawn mower development project
e-DS Mower(*e-DS: Electric-Drive System)
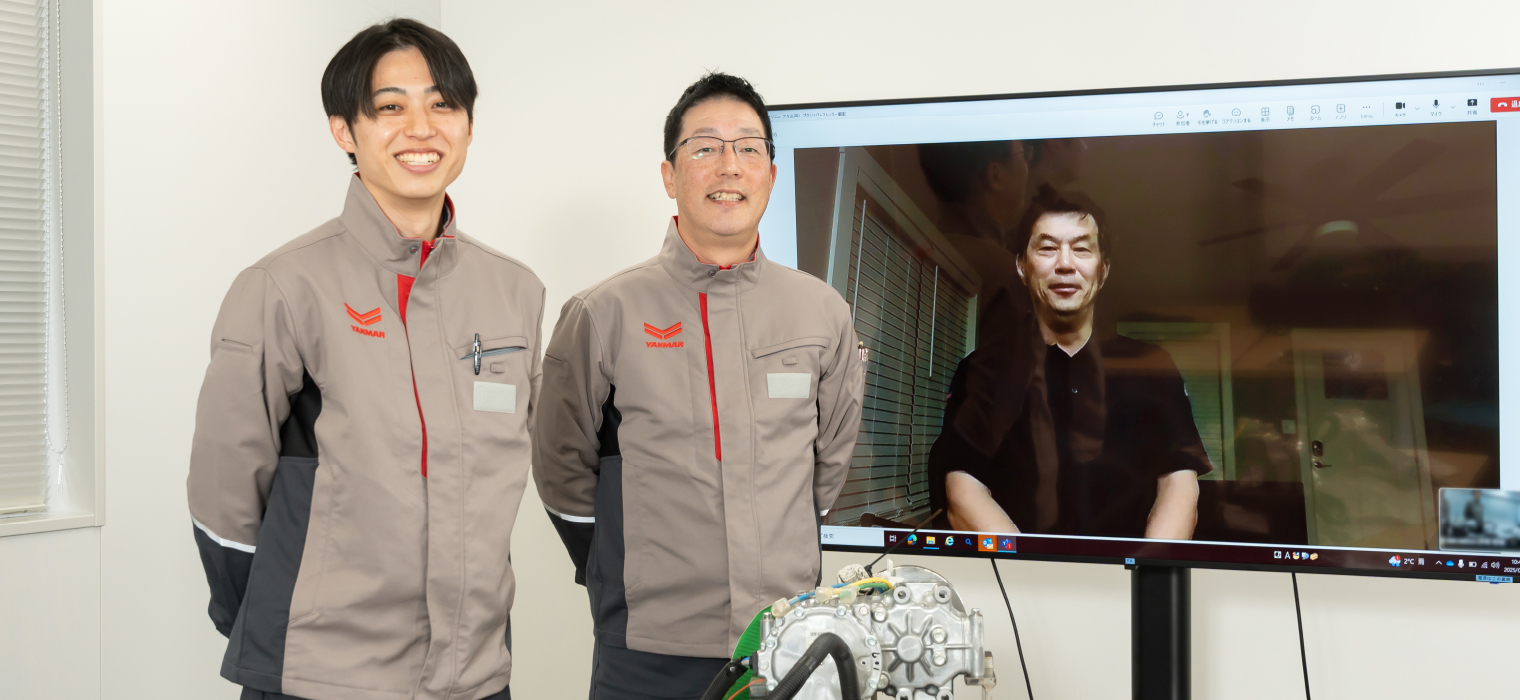
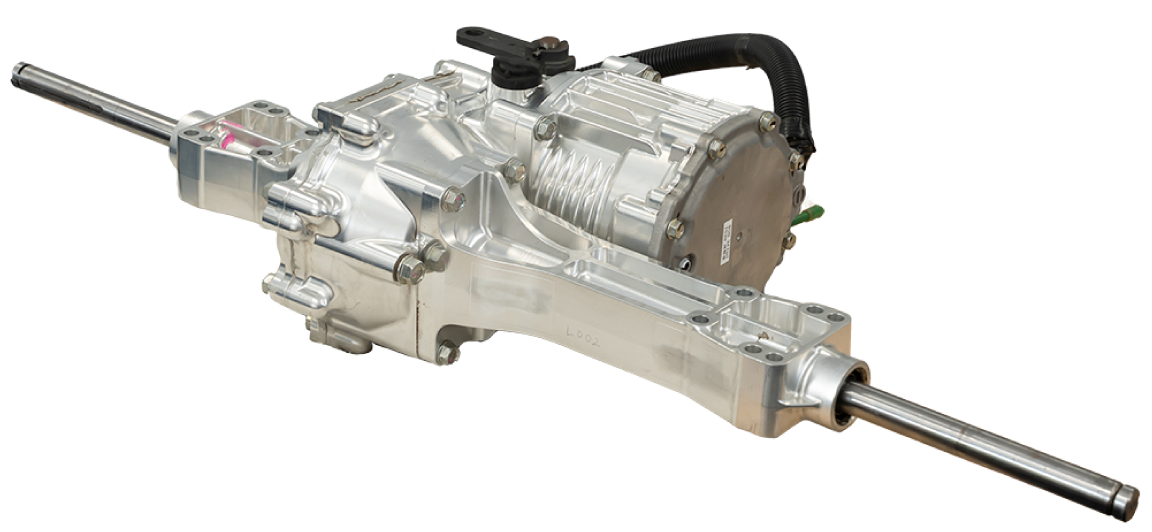
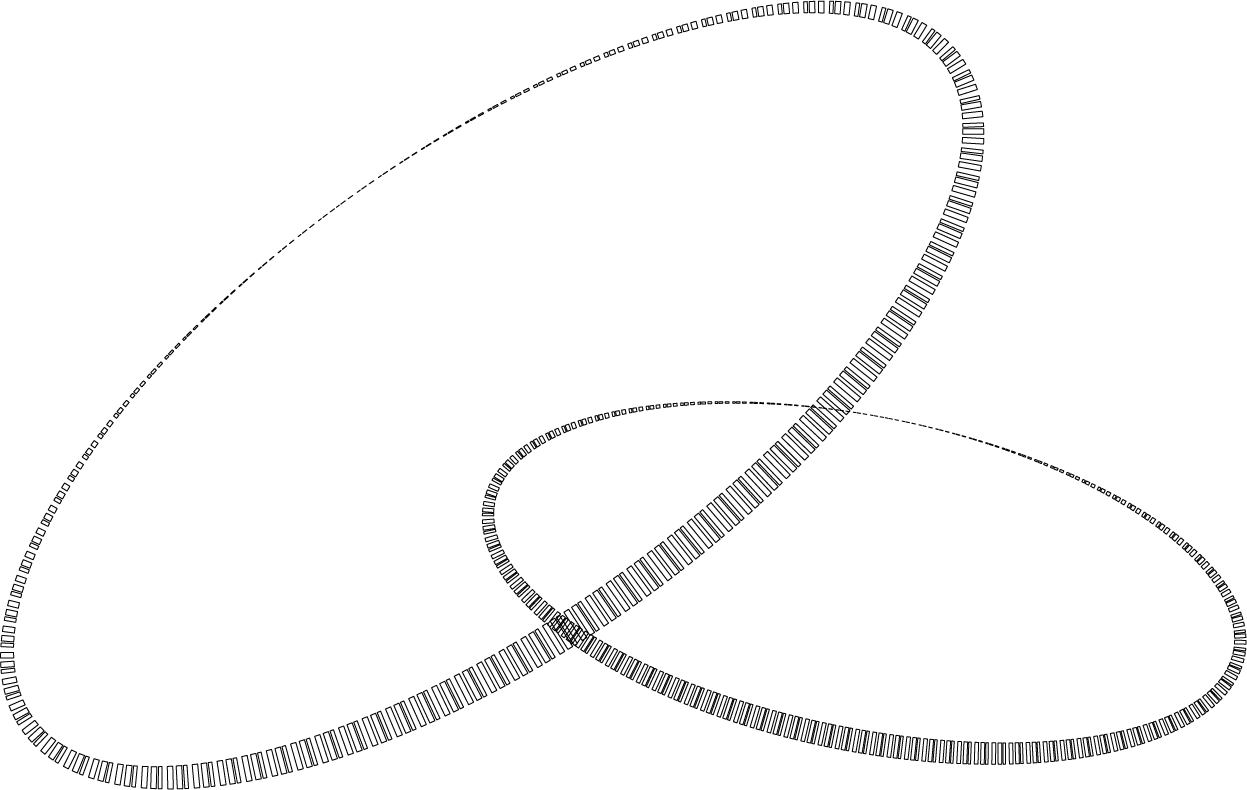
In order to reduce the environmental impact, this is the first time that KANZAKI has
Taking on the challenge of product development of electric transmission (using in-house produced electric motor)!
Transmissions are Kanzaki's core products, and among them, transmissions for mowers (riding lawn mowers) are one of our main products.
As environmental issues become more widely discussed, exhaust gas regulations are currently being strengthened in a variety of fields.
So in 2018, a project to develop an electrified mower transmission was launched.
The company initially considered sourcing electric motors from outside, but after researching more than 40 manufacturers in Taiwan, Europe, and elsewhere, it became clear that it would be impossible to achieve both quality and cost.
The decision we made at this point was to manufacture our own electric motors for the mower in-house through joint development with Yanmar's Technical Headquarters.
Interview members
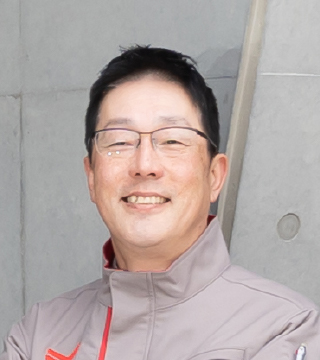
Development Department Technology Development Department
Advanced Development Group
IA
He has had a love for machines since his student days and often tinkered with motorcycles.
He joined Kanzaki Kokyukoki Seisakusho because he aspired to work in drive system design at a manufacturing company.
After working in transaxle design, quality control, and sales, he is currently promoting the mass production and lineup of electric motors for riding lawn mowers.
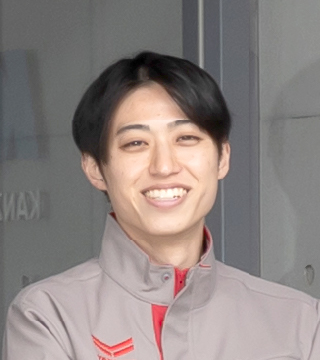
Development Department Technology Development Department
Advanced Development Group
TT
Joined the company in 2021.
He graduated from the Department of Electrical Engineering at the Faculty of Engineering.
He joined the company because he was interested in the field of power electronics and aspired to work in design at a manufacturing company.
After joining the company, he was assigned to the Development Department and, as a member of the e-DS Mower Project, was responsible for designing electric motors for riding lawn mowers.
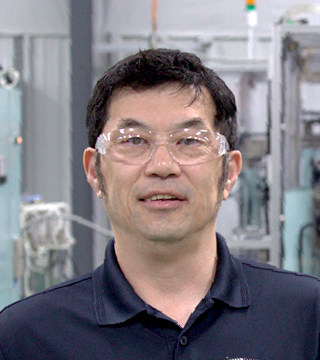
TUFF TORQ
CORPORATION
NT
Joined the company in 1998.
Hoping to find employment at a local company, he joined Kanzaki Kokyukoki Seisakusho, a well-known local company.
After joining the company, he worked in the intellectual property department, where he was involved in patent-related work for many years.
In 2015, he was transferred to the Development Department and is in charge of product planning.
In 2019, he participated in the e-DS Mower project and is currently working in the e-DS division of TUFF TORQ CORPORATION, a US subsidiary, to set up the mass production system.
The project was carried out in a trial-and-error manner
-
IAMr. Miss. -
As electrification accelerated in the mower (riding lawn mower) market, our main field, we began considering commercializing an electric transmission for mowers.
Initially, we considered procuring electric motors from outside, but as there were no electric motors that met our required specifications, we decided to produce them in-house.
However, since our main focus is on mechanical and hydraulic design and development, there were many things we did not understand, and we had a hard time doing everything, such as selecting manufacturers of the main components needed for the electric motor, including electrical components, and arranging the parts. -
NTMr. Miss. -
I researched many overseas motor manufacturers, but it was difficult to find a product that met our requirements, and we were unable to compromise on both quality and price.
So we ultimately decided to go in-house, but the most difficult part was figuring out where to start introducing the technology.
Although we contacted various companies, there were few that were willing to provide only the technology, and we were sometimes turned down just before signing a contract.
Ultimately, after much negotiation, we were able to partner with a company that was willing to help us with everything, including assembly technology, and we were finally able to move the project forward.
Looking back, I strongly believe that the key to our success was "how well we built a relationship of trust as partners." -
TTMr. Miss. -
I joined the company in fiscal 2021, but by the time performance confirmation of the prototype was completed, the performance expected at the time of design was not being achieved, and the costs were not justified.
I went to Yanmar Technical Headquarters (Central Research Institute) for two months to master motor analysis techniques, and investigated various aspects with the aim of achieving both performance and cost.
Although it has been difficult since my first year, I have been able to gain valuable experience thanks to the support of my superiors and seniors. -
IAMr. Miss. -
It was also difficult to proceed with development without a customer (the company that would manufacture and sell the machine) having been decided.
Normally, we have a set customer and create a product based on their requirements. However, this time, although we had a set target - a riding lawn mower - the customer was still undecided, so we had to grope around to come up with the detailed specifications. -
NTMr. Miss. -
Lawnmower manufacturers that used existing engines were also still in the process of finding their way around electrification, so it was difficult not only for us to provide information but also for us to exchange information that would be beneficial for both sides.
-
TTMr. Miss. -
As for assembly, since the company had no experience in manufacturing motors, there were numerous problems both during prototyping and with the mass production equipment.
We had many discussions with those in charge of manufacturing technology, quality control, and assembly to resolve each issue.
Even after the mass production equipment was transferred to TTC (TUFF TORQ CORPORATION), TTC and Kanzaki continued to work together to stabilize quality. -
NTMr. Miss. -
We had a lot of trouble when we found quality variations during final shipping testing.
KANZAKI and TTC pooled their knowledge to improve the equipment and review the assembly process, and were ultimately able to eliminate the variation.
It took about five months to resolve the issue, but we feel that the knowledge and know-how about motor manufacturing we gained during this process has become a great asset for TTC and KANZAKI.
Even if other issues arise in the future, we believe that we will be able to use our past experience to identify the cause and resolve it.
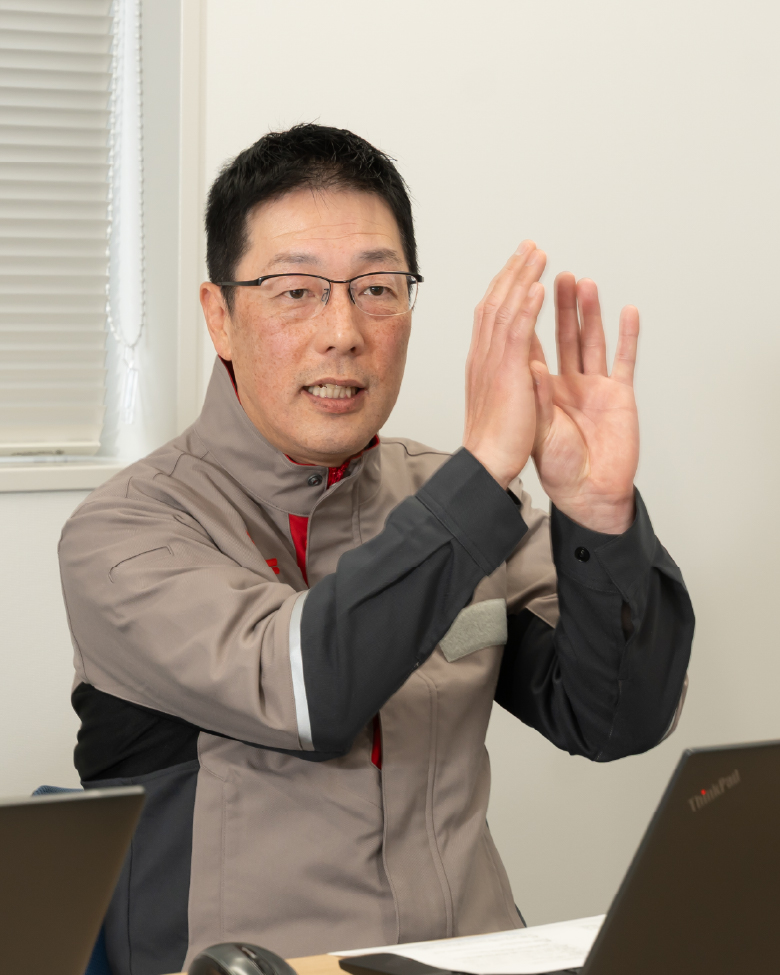
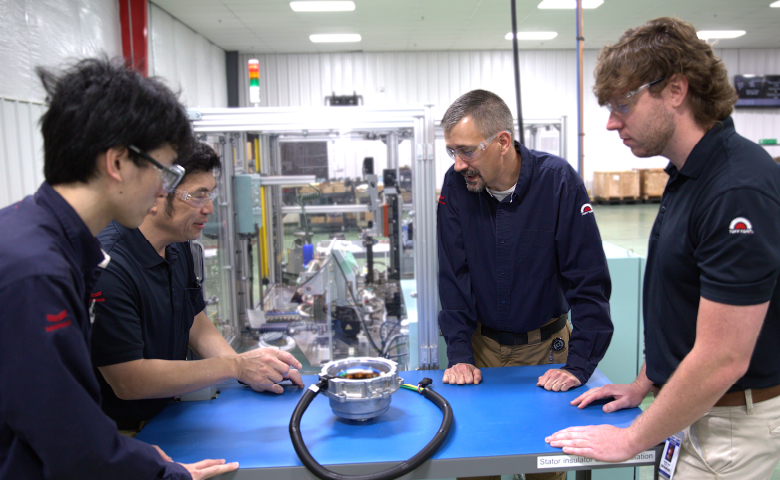
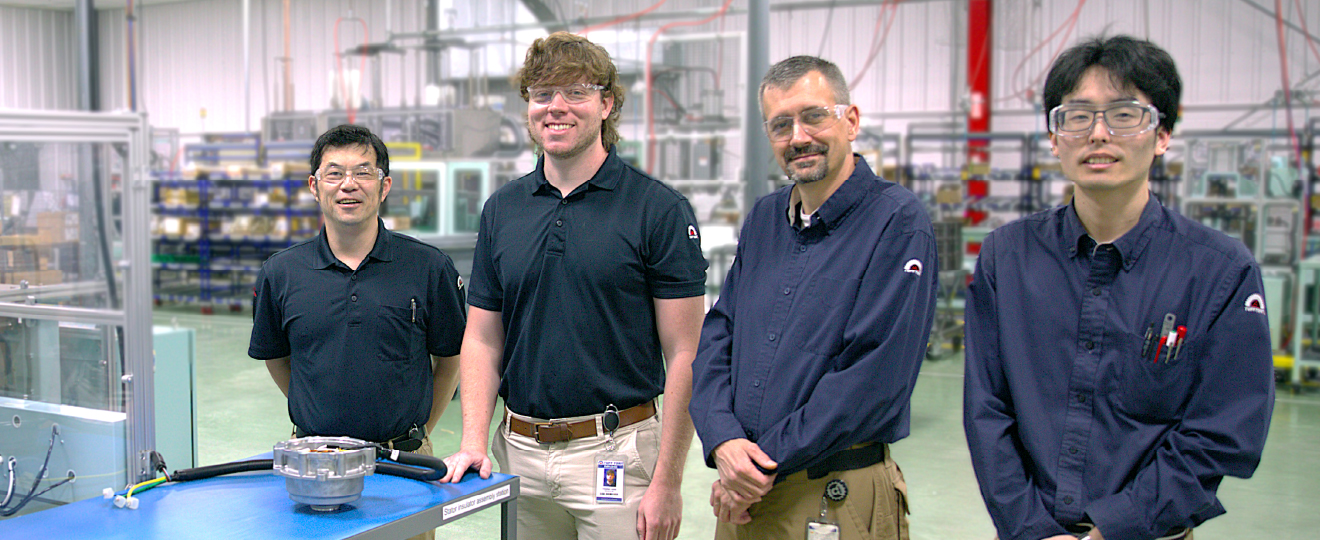
The process doesn't end with the product being completed.
Let's move on!
-
IAMr. Miss. -
Although we encountered various challenges and difficulties, through collaboration between manufacturing, procurement, sales, and development, we completed preparations for mass production of motors for e-DS mowers in March 2024, and are currently assembling motors with different output ranges to expand our lineup.
-
NTMr. Miss. -
I was so happy when it finally took shape.
We were also pleased to see that when we held a test drive of a mower equipped with our electric transmission at the exhibition, it received positive feedback for being quieter than competing machines. -
IAMr. Miss. -
Through this experience in developing electric motors, I learned that by taking into consideration the entire system, we can create electric component products that are optimal for our customers.
I would like to use this experience to expand our electrified product lineup in the future. -
TTMr. Miss. -
In the future, I would like to create even more efficient motors.
There is also an issue with it generating a lot of heat, so we would like to improve that.
Additionally, because reducing costs is an important issue, I would like to design a motor with a structure that can be manufactured in a shorter time while also taking ease of assembly into consideration. -
IAMr. Miss. -
We would like to take advantage of the technological development and experience we have gained from this electrification project, combine it with Kanzaki's core technologies of gears, transmissions and hydraulics, and continue to take on new challenges!
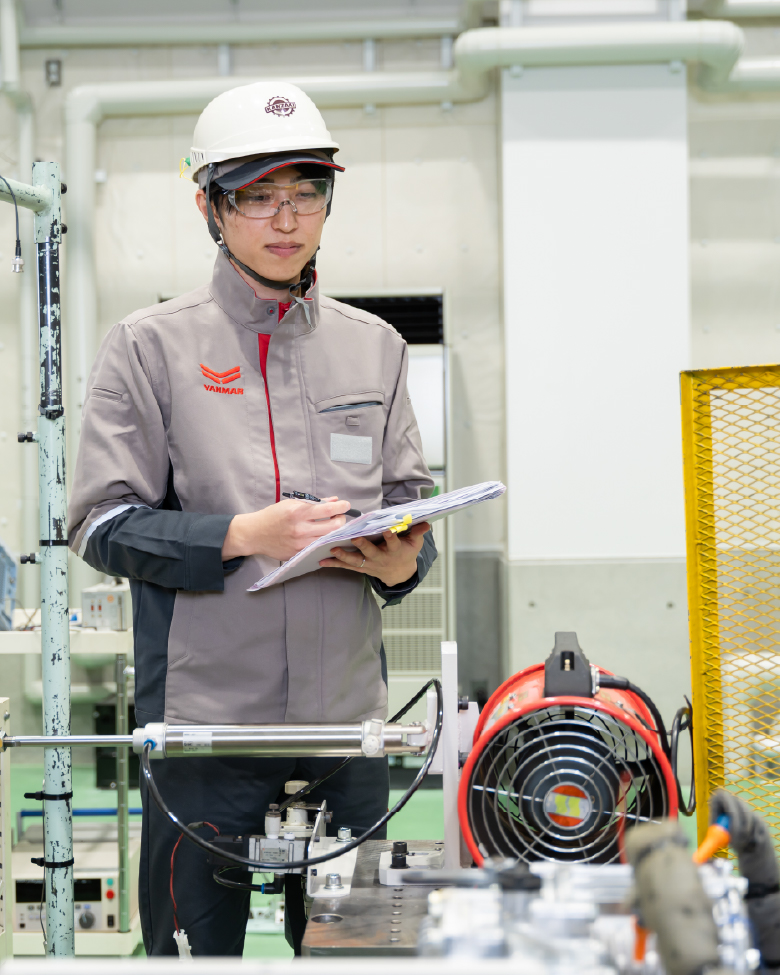
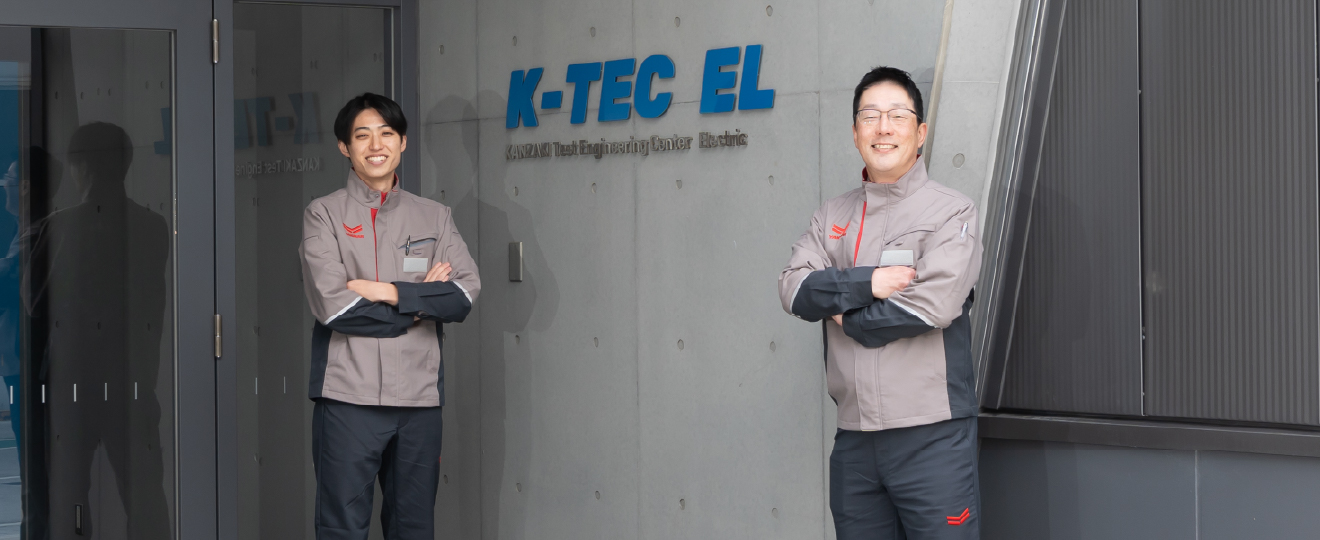
Another Story